Welding Burn Through Causes & Prevention
Introduction
In the realm of welding, achieving strong and durable joints is paramount for ensuring the integrity and longevity of structures and components. However, despite meticulous attention to detail, welders often encounter various defects that compromise the quality of their work. One such common issue is known as welding burn through.
Definition of Welding Burn Through
Welding burn through refers to a welding defect where excessive heat causes the base material to melt and create a hole or penetration through the weld joint. This occurrence typically arises when the welding parameters are not appropriately adjusted or when working with materials of varying thicknesses.
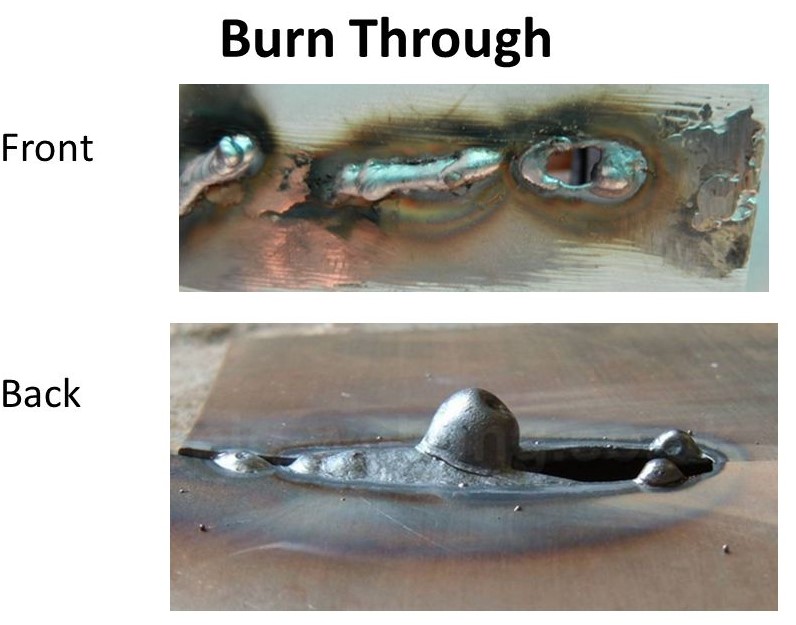
Causes of Welding Burn Through
Welding burn through can be attributed to various factors, ranging from improper welding settings to material characteristics. Understanding these causes is essential for welders to effectively prevent this defect and ensure high-quality welds.
Improper Welding Settings
One of the primary causes of welding burn through is improper welding settings. This includes inadequate adjustment of voltage, current, and travel speed during the welding process.
- Voltage and Current Settings: Incorrect voltage and current settings can lead to excessive heat generation, causing the base material to melt excessively and result in burn through. For instance, using excessively high voltage or current levels can increase heat input, while low settings may not provide sufficient penetration, both of which can contribute to burn through.
- Travel Speed: The travel speed of the welding torch plays a crucial role in controlling heat input and ensuring proper fusion between the base materials. A too slow travel speed can prolong exposure to heat, leading to burn through, whereas a too rapid speed may not allow adequate penetration, also increasing the risk of burn through.
Material Thickness and Type
The thickness and type of the base material being welded also significantly influence the likelihood of experiencing burn through.
- Thin Materials: Welding thin materials presents a challenge as they are more susceptible to overheating and burn through due to their limited heat dissipation capabilities. Special care and precise control of welding parameters are required when working with thin materials to prevent excessive heat buildup and burn through.
- Material Conductivity: The conductivity of the base material affects how efficiently it dissipates heat during welding. Materials with high thermal conductivity, such as aluminum and copper, dissipate heat more rapidly than low-conductivity materials like stainless steel or carbon steel. Failure to account for the conductivity of the material being welded can result in inadequate heat control and increased risk of burn through.
Electrode Selection and Diameter
The selection and diameter of the welding electrode play a critical role in determining heat input and distribution during the welding process.
- Electrode Material Compatibility: Different welding electrodes are designed for specific materials and welding processes. Selecting an electrode that is incompatible with the base material can lead to poor weld quality and an increased risk of burn through. It is essential to choose electrodes that are suitable for the material being welded to ensure proper fusion and minimize the risk of defects.
- Electrode Diameter and Heat Distribution: The diameter of the welding electrode directly influences the amount of heat delivered to the weld joint. A larger electrode diameter results in greater heat input, which can increase the likelihood of burn through, particularly when welding thin materials. Conversely, a smaller electrode diameter may not provide sufficient heat for proper fusion, leading to inadequate penetration and weaker welds. Achieving the right balance in electrode diameter is crucial for controlling heat distribution and preventing burn through.
Effects of Welding Burn Through
Welding burn through not only compromises the immediate integrity of the weld joint but also has broader implications that can impact the overall quality and efficiency of welding operations.
Weakened Weld Joints
One of the most immediate effects of welding burn through is the weakening of the weld joint. When excessive heat causes the base material to melt and penetrate through the weld, it creates a void or hole in the joint. This compromises the structural integrity of the weld, reducing its load-bearing capacity and resistance to mechanical stresses. Weakened weld joints are more susceptible to failure under applied loads, leading to potential safety hazards and structural failures.
Structural Integrity Concerns
Welding burn through raises significant concerns regarding the structural integrity of the welded components or structures. The presence of voids or gaps in the weld joint weakens the overall connection between the base materials, compromising the structural stability and performance of the welded assembly. In critical applications such as automotive, aerospace, or structural construction, any compromise in structural integrity due to welding defects like burn through can have severe consequences, including catastrophic failures and safety risks.
Increased Rework and Material Wastage
Dealing with welding burn through often necessitates extensive rework and material wastage, leading to increased time and costs in welding operations. Addressing burn through requires grinding out the affected area, repairing the damaged weld, and re-welding the joint to achieve the desired quality. This process not only consumes additional resources but also prolongs project timelines, delaying project completion and delivery schedules.
Prevention Techniques for Welding Burn Through
Preventing welding burn through requires a combination of proper equipment setup, meticulous material preparation, and careful electrode selection. Implementing preventive techniques can significantly reduce the risk of burn through and ensure high-quality welds.
Proper Welding Machine Setup
- Adjusting Voltage and Current: Proper adjustment of voltage and current settings on the welding machine is crucial for controlling heat input during welding. By matching the voltage and current levels to the requirements of the specific welding process and materials being welded, welders can maintain optimal heat levels and minimize the risk of burn through.
- Maintaining Consistent Travel Speed: Consistency in travel speed ensures uniform heat distribution and penetration across the weld joint. Welders should maintain a steady travel speed throughout the welding process to prevent overheating and burn through. Deviating from the optimal travel speed can result in uneven heat input and compromise weld quality.
Material Preparation and Selection
- Proper Cleaning and Preheating: Thorough cleaning of the base materials before welding removes surface contaminants and ensures better weld quality. Preheating the materials, especially when working with thick or high-conductivity metals, helps reduce thermal gradients and minimizes the risk of burn through by promoting more controlled heat input during welding.
- Selecting Appropriate Filler Materials: Choosing the right filler material is essential for achieving proper weld fusion and preventing burn through. The filler material should be compatible with the base metal and have similar mechanical properties to ensure a strong and homogeneous weld. Using filler materials with excessive heat conductivity or incompatible composition can increase the risk of burn through.
Electrode Considerations
- Matching Electrode to Base Metal: Selecting electrodes that are compatible with the base metal is critical for achieving optimal weld quality and preventing burn through. Different electrodes are designed for specific welding processes and materials, so choosing the right electrode ensures proper fusion and heat control. Matching the electrode composition and polarity to the base metal minimizes the risk of excessive heat input and burn through.
- Choosing the Right Electrode Diameter: The diameter of the welding electrode affects heat distribution and penetration during welding. Welders should choose electrodes with an appropriate diameter that matches the thickness of the base material and the desired weld penetration. Using electrodes with a larger diameter increases heat input, while smaller electrodes may not provide sufficient penetration, both of which can contribute to burn through. Achieving the right balance in electrode diameter ensures optimal heat control and reduces the risk of welding defects.
Advanced Tips and Best Practices to Mitigate Welding Burn Through
Beyond basic preventive measures, incorporating advanced techniques and best practices can further enhance weld quality and minimize the risk of burn through. Here are some advanced tips and strategies for welders
Monitoring Weld Pool Behavior
- Observation and Adjustment: Skilled welders continuously monitor the behavior of the weld pool during the welding process. By closely observing factors such as pool size, shape, and fluidity, welders can assess heat input and penetration depth in real-time. This allows for on-the-fly adjustments to welding parameters, such as voltage, current, and travel speed, to maintain optimal heat control and prevent burn through.
- Utilizing Welding Cameras and Sensors: Welding cameras and sensors provide valuable insights into weld pool behavior, offering visual and quantitative data for analysis. These technologies enable welders to identify potential issues such as overheating or inadequate penetration early on, allowing for timely interventions to prevent burn through and ensure consistent weld quality.
Implementing Shielding Gas Effectively
- Choosing the Right Shielding Gas: Selecting the appropriate shielding gas for the welding process and materials is essential for preventing atmospheric contamination and ensuring proper arc stability. Different gases, such as argon, carbon dioxide, and mixtures thereof, offer varying levels of protection and influence weld characteristics. By selecting the right shielding gas composition and flow rate, welders can create an optimal welding environment that minimizes the risk of burn through and enhances weld quality.
- Maintaining Gas Flow and Coverage: Proper gas flow and coverage are critical for effective shielding and preventing atmospheric contamination during welding. Welders should ensure that the gas flow rate is sufficient to provide adequate coverage over the weld zone, especially when working with reactive metals or in windy environments. Additionally, maintaining consistent gas flow and distribution helps stabilize the arc and promote smooth weld bead formation, reducing the likelihood of burn through and other defects.
Employing Welding Techniques to Mitigate Burn Through
- Pulse Welding: Pulse welding techniques, such as pulse current or pulse frequency modulation, offer precise control over heat input and penetration depth. By pulsing the welding current at predetermined intervals, welders can effectively manage heat buildup and minimize the risk of burn through, particularly when welding thin or heat-sensitive materials.
- Backstepping and Stitch Welding: Backstepping involves welding in a reverse direction, starting from the completed portion of the weld joint and progressing towards the beginning. This technique helps dissipate heat and reduces the likelihood of burn through by limiting prolonged exposure to heat. Similarly, stitch welding involves breaking up long weld runs into smaller segments, allowing for better heat control and minimizing the risk of overheating and burn through.
FAQs
Is welding burn through common?
Welding burn through can occur, but with proper precautions, it can be minimized.
Can DIY welders prevent burn through?
Yes, DIY welders can prevent burn through by following proper guidelines and techniques.
How does welding burn through impact project costs?
Welding burn through can lead to project delays, increasing overall costs.
Are there eco-friendly welding practices?
Yes, advancements in welding technology include eco-friendly practices to minimize environmental impact.
What industries are most affected by welding burn through?
Industries like aerospace, automotive, and construction may face unique challenges related to welding burn through.
Conclusion
In wrapping up our exploration of welding burn through, it’s evident that proactive prevention is the key to a successful welding experience. Whether you’re a seasoned professional or a DIY enthusiast, understanding the causes, implementing preventive measures, and staying updated on technological advancements are crucial.