Introduction
In the shipbuilding industry, welding plays a crucial role in constructing and maintaining vessels of various sizes and types. Welding is a process that joins metals together, ensuring structural integrity and enhancing the overall safety and performance of ships. This article delves into the significance of welding in the shipbuilding industry, its different techniques, challenges faced, and its impact on ship construction.
Understanding Welding in Shipbuilding
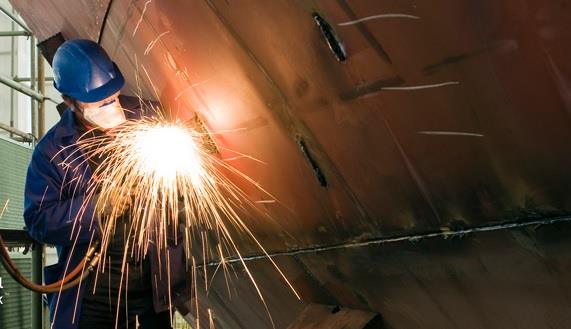
What is Welding?
Welding is a fabrication process that involves joining metals together through fusion. In shipbuilding, welding is utilized to create strong and continuous bonds between various steel components. It ensures the structural integrity of the vessel, making it capable of withstanding harsh marine conditions.
Importance of Welding in Shipbuilding
Welding is a fundamental aspect of ship construction as it provides the necessary strength and durability to the ship’s structure. Properly executed welds are essential for the vessel’s safety and longevity. Without welding, it would be nearly impossible to build large ships that can transport goods and passengers across the oceans.
Types of Welding Techniques Used in Shipbuilding
The shipbuilding industry employs various welding techniques, each suited for specific applications and materials.
Shielded Metal Arc Welding (SMAW)
SMAW, commonly known as stick welding, is a versatile welding process widely used in shipyards. It involves using a consumable electrode coated in flux to create the weld. SMAW is suitable for both thick and thin plates and can be utilized in all positions.
Gas Metal Arc Welding (GMAW)
GMAW, also known as MIG (Metal Inert Gas) welding, employs a continuous solid wire electrode and a shielding gas to protect the weld pool. It is highly efficient and finds extensive usage in shipbuilding due to its speed and ease of automation.
Flux-Cored Arc Welding (FCAW)
FCAW is similar to GMAW but uses a flux-cored electrode, eliminating the need for an external shielding gas. This process is well-suited for shipyards dealing with thick materials and adverse weather conditions.
Submerged Arc Welding (SAW)
SAW is a high-productivity welding process that involves a continuous wire electrode and a granular flux. It is commonly used for welding thick steel plates in shipbuilding.
Electron Beam Welding (EBW)
EBW is a precise welding process that uses a focused beam of high-velocity electrons to create the weld. It is often employed for critical joints in ship components that require utmost precision.
Friction Stir Welding (FSW)
FSW is a solid-state welding technique that joins materials through frictional heat generated by a rotating tool. It is commonly used for aluminum and other non-ferrous materials in the shipbuilding industry.
Welding Automation in Shipbuilding
As the shipbuilding industry embraces automation, welding processes are also being automated to improve efficiency and quality.
Advantages of Welding Automation
Welding automation offers several benefits, including increased productivity, consistency in weld quality, and reduced labor costs. Automated systems can work non-stop, leading to faster ship construction.
Challenges and Considerations
Implementing welding automation requires substantial investment and careful planning. Skilled personnel are needed to operate and maintain automated welding systems. Additionally, the compatibility of automation with various welding techniques must be considered.
Ensuring Weld Quality in Shipbuilding
Maintaining weld quality is crucial to ensure the structural integrity and safety of ships.
Non-Destructive Testing (NDT) Methods
NDT methods, such as ultrasonic testing and X-ray inspection, are employed to detect defects or discontinuities in welds without damaging the material. These tests help identify and rectify potential issues before they compromise the ship’s integrity.
Quality Control Measures
Shipyards adhere to strict quality control measures to ensure that welding procedures meet international standards and regulations. Regular inspections and welder qualifications are part of this comprehensive quality control process.
Environmental and Safety Concerns in Shipyard Welding
Shipyard welding can pose environmental and safety challenges that need to be addressed.
Emission Control
Welding fumes and emissions can be hazardous to workers and the environment. Shipyards implement exhaust systems and enforce proper ventilation to minimize exposure.
Personal Protective Equipment (PPE)
Welders are required to wear appropriate PPE, including welding helmets, gloves, and protective clothing, to safeguard against arc flashes and other welding-related hazards.
Welding Dissimilar Materials in Shipbuilding
In ship construction, different materials may need to be joined together.
Techniques for Joining Different Metals
Welding dissimilar materials requires specialized techniques, such as mechanical fastening, hybrid welding processes, and the use of interlayers.
The Impact of Automation on Shipbuilding Industry Jobs
The integration of automation in shipyards raises concerns about its impact on the workforce.
Pros and Cons of Welding Automation
While welding automation improves efficiency, it may lead to a reduced demand for manual welders. On the other hand, automation creates new job opportunities in operating and maintaining automated systems.
Emerging Trends in Shipbuilding Welding
Innovative technologies are reshaping the shipbuilding industry, including welding practices.
Additive Manufacturing in Welding
Additive manufacturing, or 3D printing, is being explored as a viable method for producing intricate ship components, reducing material wastage, and streamlining the manufacturing process.
Artificial Intelligence and Robotics Integration
AI and robotics are revolutionizing shipyard operations, including welding tasks. AI-powered systems can optimize welding parameters and detect defects with unparalleled accuracy.
Welding Education and Training in the Shipbuilding Sector
Addressing the skill gap is essential to sustain a skilled workforce in shipbuilding.
Apprenticeship Programs
Apprenticeship programs play a vital role in training the next generation of welders. These programs combine classroom instruction with hands-on experience in shipyards.
The Future of Welding in Shipbuilding
As technology continues to advance, the future of welding in the shipbuilding industry looks promising.
Technological Advancements
Continuous advancements in welding technology will lead to faster, more precise, and efficient welding processes, enhancing shipbuilding capabilities.
Sustainability Initiatives
The shipbuilding industry is also embracing sustainability practices, including eco-friendly welding techniques and the use of recycled materials.
FAQs
Is welding the only method used to join ship components?
While welding is a predominant method, shipyards also utilize mechanical fastening, adhesive bonding, and hybrid welding processes for specific applications.
Are there any environmentally friendly welding methods?
Yes, techniques like friction stir welding and laser welding produce fewer emissions and contribute to a more sustainable shipbuilding process.
What role does artificial intelligence play in welding automation?
AI helps optimize welding parameters, monitor weld quality, and identify defects, leading to improved efficiency and reduced material wastage.
How can individuals pursue a welding career in the shipbuilding industry?
Aspiring welders can enroll in welding apprenticeship programs or attend vocational schools that offer specialized shipbuilding welding courses.
What are some notable challenges in welding dissimilar materials?
Welding different materials can result in differing thermal expansion rates and metallurgical properties, requiring careful selection of appropriate welding techniques.
Conclusion
Welding is the backbone of the shipbuilding industry, providing the strength and reliability required for marine vessels to navigate the world’s waters. As the industry moves forward, welding automation, innovative techniques, and a skilled workforce will shape the future of shipbuilding. Embracing cutting-edge technologies while maintaining a focus on safety and quality will lead to a greener, more efficient, and resilient shipbuilding sector.