Welding Non-Ferrous Metals: Techniques, Applications, and Challenges
Introduction
Welding is a critical manufacturing process that joins materials together to create strong and durable structures. While welding is often associated with ferrous metals like steel and iron, it is equally essential for non-ferrous metals, such as aluminum, copper, and titanium. Non-ferrous metals possess unique properties and applications that require specific welding techniques. In this comprehensive guide, we will delve into the world of welding non-ferrous metals, exploring the techniques, applications, challenges, and the future of this important field.
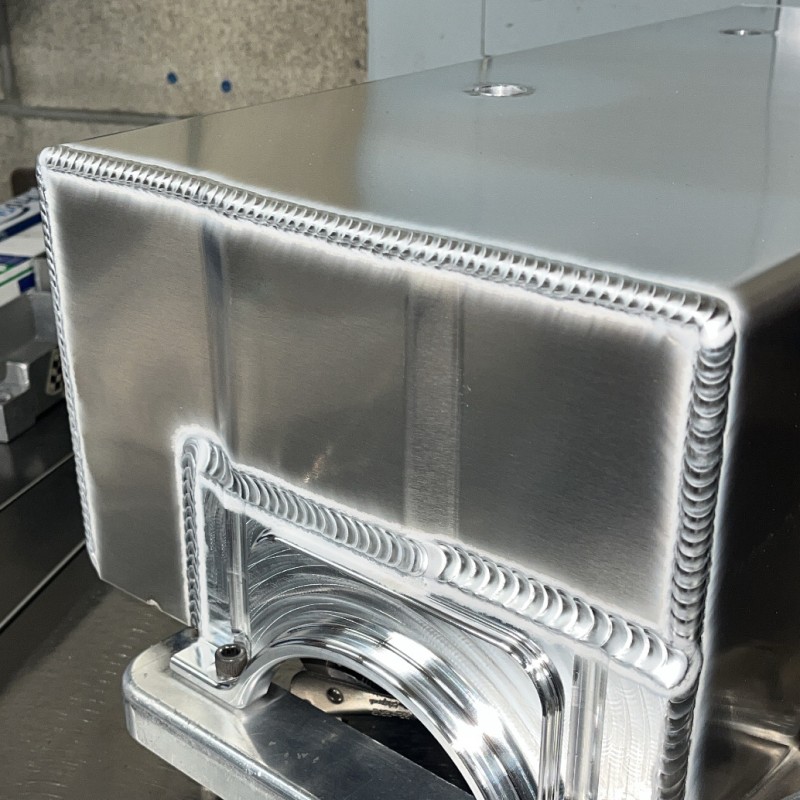
Understanding Non-Ferrous Metals
Non-ferrous metals are metals that do not contain iron as a primary component. They offer various advantages over ferrous metals, including high corrosion resistance, excellent electrical and thermal conductivity, and lightweight properties. Some common non-ferrous metals used in various industries include aluminum, copper, titanium, nickel, and zinc.
Aluminum Welding
Aluminum is one of the most widely used non-ferrous metals in manufacturing due to its low density, corrosion resistance, and excellent thermal conductivity. However, welding aluminum presents unique challenges, primarily because of its low melting point (660.32°C or 1220.58°F) and high thermal conductivity.
Techniques for Welding Aluminum
- Gas Tungsten Arc Welding (GTAW/TIG): TIG welding is the most common method for welding aluminum. It uses a non-consumable tungsten electrode to create a controlled and precise arc, while a separate filler rod is added to the weld pool as needed. TIG welding offers excellent control and produces high-quality welds, making it suitable for a wide range of applications, from aerospace to automotive.
- Gas Metal Arc Welding (GMAW/MIG): MIG welding is another popular method for aluminum welding. It uses a consumable wire electrode fed through a welding gun, along with a shielding gas, typically argon, to protect the weld area from contamination. MIG welding is faster than TIG welding and is often used in industries where speed is essential.
- Friction Stir Welding (FSW): FSW is a solid-state welding process that is ideal for joining aluminum and other non-ferrous materials. It involves a rotating, non-consumable pin that creates friction and heat, softening the material and forming a weld. FSW is commonly used in the aerospace and automotive industries for its ability to produce high-strength, defect-free joints.
- Resistance Spot Welding: This method is commonly used for joining thin sheets of aluminum. It involves applying an electric current to the metal pieces, creating heat at the contact points. When the pieces are pressed together, they fuse, forming a spot weld. It is used extensively in the automotive industry for body panel assembly.
Copper Welding
Copper is renowned for its exceptional electrical conductivity and corrosion resistance, making it a crucial material in electrical and electronic applications. Copper welding techniques vary depending on the specific type of copper being used.
Techniques for Welding Copper
- Gas Tungsten Arc Welding (GTAW/TIG): TIG welding is also suitable for copper welding. It allows for precise control over the welding process, ensuring high-quality welds. TIG welding is commonly used for applications like heat exchangers, electrical connectors, and plumbing.
- Gas Metal Arc Welding (GMAW/MIG): MIG welding can be employed for welding copper, although it is less common than TIG welding. The process requires careful control of the welding parameters to prevent overheating and ensure a sound weld.
- Resistance Welding: Resistance welding methods, such as spot welding and seam welding, are often used for joining copper in electrical and electronic applications. These methods provide efficient and precise welding of copper components.
Titanium Welding
Titanium is a lightweight, corrosion-resistant metal commonly used in aerospace, medical, and chemical processing industries. Welding titanium presents challenges due to its high reactivity with oxygen and nitrogen at elevated temperatures.
Techniques for Welding Titanium
- Gas Tungsten Arc Welding (GTAW/TIG): TIG welding is the preferred method for welding titanium. It requires the use of a high-purity argon shielding gas to protect the weld from contamination. Special precautions, such as back-purging with argon, are often taken to maintain a clean weld environment.
- Plasma Arc Welding (PAW): PAW is a variation of TIG welding that uses a constricted plasma arc for higher energy density. It can be used for welding thicker titanium sections, offering better penetration and faster welding speeds.
- Electron Beam Welding (EBW): EBW is a high-energy welding process that uses a focused beam of electrons to melt and join titanium. It is commonly used in aerospace applications due to its ability to produce high-quality, deep welds.
Nickel Welding
Nickel and its alloys are known for their high-temperature strength, corrosion resistance, and excellent performance in extreme environments, making them crucial in the aerospace and petrochemical industries.
Techniques for Welding Nickel
- Gas Tungsten Arc Welding (GTAW/TIG): TIG welding is commonly used for nickel and its alloys. It allows for precise control of the welding process and is suitable for welding thin nickel components.
- Shielded Metal Arc Welding (SMAW): SMAW, or stick welding, can be used for nickel welding when TIG welding is not feasible. It involves a coated electrode that provides both the filler material and the shielding gas.
- Gas Metal Arc Welding (GMAW/MIG): MIG welding can be employed for nickel alloys, particularly for thicker sections. Care must be taken to select the appropriate filler wire and shielding gas to prevent weld contamination.
Zinc Welding
Zinc is often used as a protective coating for steel (galvanized steel) to prevent corrosion. While zinc welding is not as common as other non-ferrous metals, it is essential for maintaining the integrity of galvanized steel structures.
Techniques for Welding Zinc
- Gas Metal Arc Welding (GMAW/MIG): MIG welding is commonly used for welding galvanized steel. The welding process requires specialized techniques to minimize the release of zinc fumes, which can be harmful if inhaled.
- Resistance Spot Welding: Spot welding is used for joining thin sheets of galvanized steel in applications like automotive manufacturing and HVAC systems.
Common Challenges in Welding Non-Ferrous Metals
Welding non-ferrous metals presents unique challenges compared to welding ferrous metals. These challenges are primarily due to the lower melting points, higher thermal conductivity, and increased sensitivity to atmospheric contaminants of non-ferrous materials. Some common challenges include:
- Oxidation and Contamination: Non-ferrous metals, especially aluminum and titanium, are highly reactive with oxygen at elevated temperatures. To counter this, welding processes often require the use of inert shielding gases like argon and specialized techniques such as back-purging.
- Dissimilar Metal Welding: Non-ferrous metals are frequently joined with other non-ferrous materials or even ferrous metals. Welding dissimilar metals can be challenging due to differences in melting points, thermal expansion rates, and metallurgical compatibility.
- Thermal Conductivity: Non-ferrous metals, particularly copper and aluminum, have high thermal conductivity. This property can result in rapid heat dissipation, making it challenging to achieve and maintain the necessary welding temperatures.
- Fusion and Cracking: Non-ferrous metals are susceptible to weld defects like lack of fusion and cracking, especially if not welded with the proper techniques and parameters.
- Filler Material Selection: Choosing the right filler material is crucial in non-ferrous metal welding. The filler material must match the base metal’s composition and properties to ensure a strong and reliable weld.
Applications of Welding Non-Ferrous Metals
Non-ferrous metals play a vital role in various industries, and welding is indispensable for fabricating components and structures using these materials. Here are some notable applications:
- Aerospace Industry: Aluminum and titanium are extensively used in aircraft construction. Welding non-ferrous materials is crucial for assembling airframes, engine components, and structural parts.
- Automotive Industry: Welding of non-ferrous metals is essential in the automotive sector for manufacturing lightweight, fuel-efficient vehicles. Aluminum, in particular, is used for body panels, engine blocks, and suspension components.
- Electrical and Electronics: Copper is a key material for electrical wiring and electronic components. Welding is used to join copper conductors and create reliable connections in electrical systems.
- Chemical and Petrochemical Industry: Nickel alloys are employed in chemical processing equipment due to their corrosion resistance. Welding is essential for fabricating vessels, pipelines, and reactors used in these industries.
- Medical Devices: Titanium’s biocompatibility and corrosion resistance make it ideal for medical implants and devices. Welding is used to create precise and durable joints in medical equipment and implants.
- Shipbuilding: Aluminum is often used in ship construction to reduce weight and improve fuel efficiency. Welding non-ferrous materials is critical for building hulls, superstructures, and other ship components.
- Construction: In architectural applications, aluminum is used for windows, doors, and curtain walls. Welding ensures the structural integrity and durability of these components.
- Heat Exchangers: Copper and aluminum are frequently used in heat exchanger fabrication. Welding is essential for creating efficient and leak-free heat transfer surfaces.
Future Trends in Non-Ferrous Metal Welding
The field of welding non-ferrous metals continues to evolve, driven by advancements in materials, technologies, and industry demands. Some future trends and developments to watch for include:
- Advanced Welding Techniques: Continued research into advanced welding techniques, such as laser welding and electron beam welding, will improve the precision and efficiency of non-ferrous metal welding processes.
- Materials Innovation: The development of new non-ferrous alloys and composites will create opportunities for novel applications. Welding processes will need to adapt to accommodate these materials.
- Automation and Robotics: Automation and robotics are becoming increasingly important in non-ferrous metal welding, especially in industries like aerospace and automotive. These technologies offer improved repeatability and reduced labor costs.
- Additive Manufacturing: Metal additive manufacturing, or 3D printing, is gaining traction in industries that use non-ferrous metals. Developing reliable welding techniques for post-processing and joining 3D-printed parts will be essential.
- Environmentally Friendly Welding: There is a growing emphasis on environmentally friendly welding processes, including those that reduce energy consumption, emissions, and waste in non-ferrous metal welding.
- Digitalization and Data Analytics: The integration of digital tools and data analytics in welding processes will enable real-time monitoring, quality control, and predictive maintenance, enhancing the overall efficiency and reliability of non-ferrous metal welding operations.
FAQs
Can I weld aluminum with a standard welding machine?
Yes, you can weld aluminum with a standard welding machine, but it’s recommended to use a TIG welder for better results. Aluminum welding requires precise control over heat and a clean, oxide-free surface, which TIG welding excels at.
What’s the best way to prevent warping when welding copper?
To prevent warping when welding copper, preheat the material evenly before welding and use a low-heat input technique. Additionally, employing a heat sink near the weld area can help dissipate excess heat and reduce distortion.
Are there any health risks associated with welding non-ferrous metals?
Welding non-ferrous metals can produce harmful fumes, including metal oxide particles. It’s crucial to work in a well-ventilated area and wear appropriate respiratory protection to minimize health risks.
Can I weld different non-ferrous metals together?
Yes, you can weld different non-ferrous metals together, but it requires specialized techniques and filler materials. Consult with an experienced welder or engineer for guidance on welding dissimilar metals.
What is the primary advantage of using non-ferrous metals in construction?
The primary advantage of using non-ferrous metals in construction is their resistance to corrosion. Non-ferrous metals like aluminum and copper can withstand harsh environmental conditions, making them ideal for outdoor and marine applications.
How can I improve the aesthetics of my non-ferrous metal welds?
Achieving aesthetically pleasing non-ferrous metal welds involves proper cleaning and finishing. After welding, clean the weld bead thoroughly and use techniques such as brushing or polishing to enhance the appearance.
Conclusion
Welding non-ferrous metals is a critical process that plays a pivotal role in various industries, from aerospace and automotive to electronics and construction. Each type of non-ferrous metal presents its own unique challenges and requires specific welding techniques to achieve strong, reliable, and defect-free welds. As technology continues to advance, the field of welding non-ferrous metals will evolve to meet the demands of modern industry, creating opportunities for innovation and growth in this essential sector of manufacturing.