Welding Techniques for Cast Iron
Introduction
Welding is a fundamental process in the world of manufacturing and construction, enabling the joining of diverse materials to create robust and intricate structures. Among the various materials that welders encounter, cast iron holds a unique position due to its distinct properties and challenges during the welding process. Cast iron, an iron-carbon alloy with a higher carbon content than steel, is renowned for its hardness, excellent castability, and wear resistance, making it indispensable in countless industrial applications. Welding cast iron demands specialized techniques and expertise due to its brittleness, low ductility, and susceptibility to cracking. Improper welding practices can result in defective welds, compromising the structural integrity and performance of the welded components. Therefore, understanding the nuances of cast iron welding and employing the right welding processes and best practices become paramount for achieving high-quality, durable welds.
Definition and Properties of Cast Iron
Cast iron is a group of iron-carbon alloys that contains a higher carbon content than steel, typically ranging from 2% to 4%. This carbon content contributes to its unique properties, including high hardness, excellent castability, and good wear resistance. Cast iron is commonly used in various industries for manufacturing engine blocks, pipes, gears, and other components.
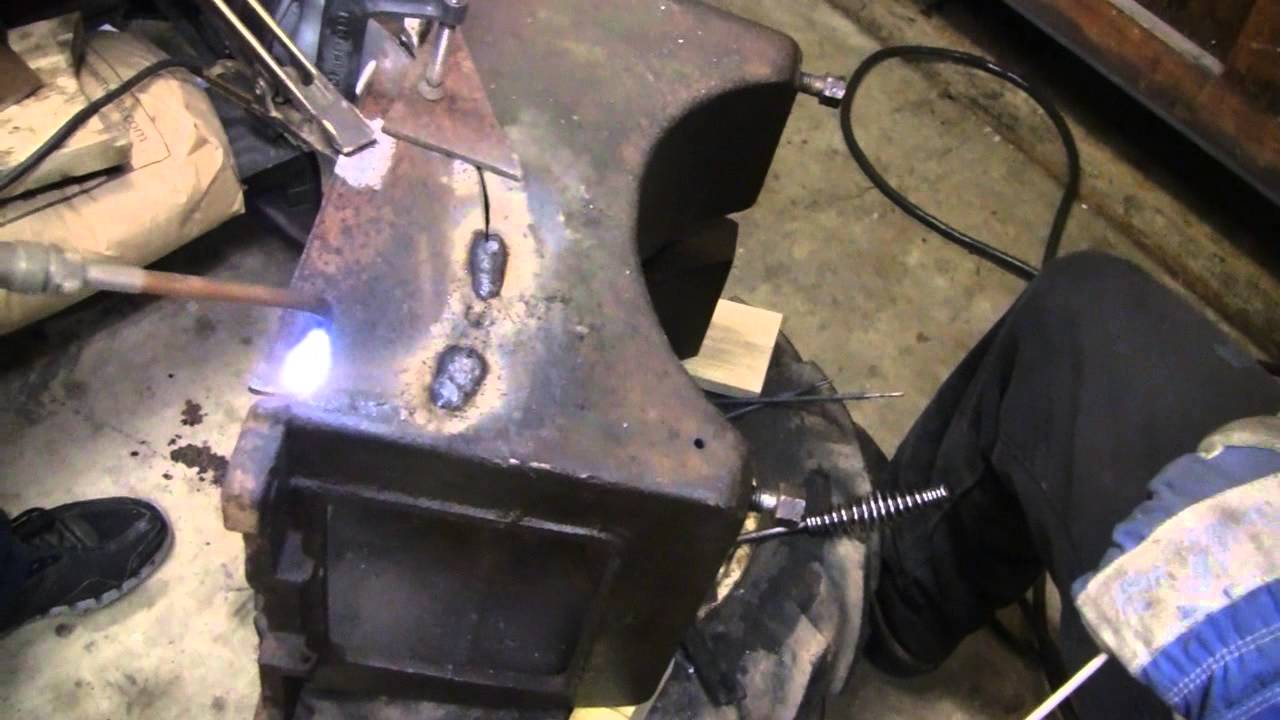
Challenges in Welding Cast Iron
Welding cast iron poses several challenges due to its composition and properties. The main difficulties include:
- High carbon content: Cast iron’s high carbon content makes it susceptible to cracking during the welding process.
- Brittle nature: Cast iron is inherently brittle, making it prone to fracture if not handled carefully during welding.
- Limited ductility: The lack of ductility can lead to significant distortion and difficulty in achieving proper weld joint integrity.
- Thermal conductivity: Cast iron has low thermal conductivity, which can result in rapid cooling and contraction during welding, leading to cracks.
Importance of Proper Welding Techniques for Cast Iron
Proper welding techniques are crucial for cast iron to achieve strong, reliable welds with minimal defects. High-quality welding ensures the integrity and longevity of the welded components, reducing the risk of failure and costly repairs. Welding techniques tailored to cast iron’s specific properties can mitigate its inherent challenges, resulting in successful welds and increased operational efficiency.
Understanding Cast Iron Welding Processes
Preheating and Post-Weld Heat Treatment
Preheating is a vital step in cast iron welding to reduce thermal shock and minimize cracking. Post-weld heat treatment, such as stress relieving or annealing, helps alleviate residual stresses and improves the weld’s overall strength and ductility.
Selecting the Right Welding Process
Different welding processes are available for cast iron, each with its advantages and limitations:
- Oxy-Acetylene Welding: Oxy-acetylene welding utilizes a flame produced by burning acetylene gas in oxygen to generate the required heat for welding cast iron.
- Shielded Metal Arc Welding (SMAW): SMAW, also known as stick welding, employs consumable electrodes coated with flux to shield the weld pool from atmospheric contamination.
- Gas Metal Arc Welding (GMAW/MIG): GMAW uses a continuously fed consumable wire electrode and a shielding gas to protect the weld from the atmosphere.
- Flux-Cored Arc Welding (FCAW): FCAW is similar to GMAW, but the electrode has a flux core, eliminating the need for an external shielding gas.
- Tungsten Inert Gas Welding (TIG): TIG welding uses a non-consumable tungsten electrode and an inert gas, such as argon, to shield the weld pool.
Benefits and Limitations of Each Welding Process for Cast Iron
Each welding process has its benefits and limitations when applied to cast iron. For example:
- Oxy-acetylene welding provides precise heat control but may be slower.
- SMAW is versatile but may require more post-weld processing.
- GMAW and FCAW offer higher deposition rates, but proper shielding is crucial.
- TIG welding provides precise control but demands skilled operators.
Pre-Welding Preparations
Inspection and Preparation of the Cast Iron Part
Before welding, the cast iron part should be thoroughly inspected for cracks, impurities, and any defects that might affect the weld quality. Proper cleaning and preparation of the welding area are essential to ensure good fusion and reduce the risk of contamination.
Pre-Cleaning and Removal of Impurities
Cast iron surfaces must be thoroughly cleaned to remove any contaminants like grease, oil, paint, or rust. Mechanical methods such as wire brushing or grinding are often used.
Ensuring Proper Fit-up and Joint Preparation
Proper fit-up and joint preparation are critical to achieving successful welds. Beveling, chamfering, or other appropriate joint preparations must be carried out to create suitable weld groove configurations.
Selection of Suitable Filler Materials
The choice of filler material is crucial in cast iron welding. Nickel-based or nickel-iron electrodes are commonly used for their ability to match the properties of cast iron and minimize cracking.
Welding Techniques for Cast Iron
Oxy-Acetylene Welding for Cast Iron
- Setup and Equipment: Oxy-acetylene welding requires an oxy-fuel torch, acetylene and oxygen tanks, and appropriate safety gear.
- Flame Adjustments and Neutral Flame: The welding flame must be adjusted to a neutral or slightly carburizing flame to avoid excess carbon absorption and minimize cracking.
- Welding Procedure and Techniques: The welder must preheat the cast iron part evenly and maintain the proper heat throughout the welding process. The filler material is added gradually while moving the torch to create a sound weld.
- Advantages and Limitations: Oxy-acetylene welding provides precise heat control and is suitable for thin sections. However, it is relatively slow and may not be suitable for thicker cast iron components.
Shielded Metal Arc Welding (SMAW) for Cast Iron
- Electrode Selection for Cast Iron Welding: Specialized iron-cast nickel electrodes are commonly used for SMAW on cast iron due to their ability to match the cast iron properties.
- Preheating Requirements: Preheating is essential to minimize cracking. The cast iron part should be preheated to a specific temperature range before welding.
- Welding Procedure and Techniques: Welders should use short arc lengths, low amperage settings, and a weaving motion to prevent overheating and distortion. Peening the weld bead while it is still hot can also reduce residual stresses.
- Post-Weld Heat Treatment Considerations: Stress-relieving post-weld heat treatment is often necessary to improve the weld’s ductility and reduce internal stresses.
Gas Metal Arc Welding (GMAW/MIG) for Cast Iron
- Selection of Suitable Shielding Gases: A mixture of argon and helium or argon and carbon dioxide is typically used as the shielding gas for GMAW on cast iron.
- Preheating and Interpass Temperature Control: Preheating the cast iron and controlling the interpass temperature are crucial to prevent cracking and enhance weld quality.
- Welding Techniques and Parameters: GMAW requires a controlled welding speed and proper manipulation of the torch to achieve good fusion and minimize heat input.
- Precautions to Avoid Cracking and Distortion: Employing proper preheating, controlling heat input, and using suitable filler material are essential in preventing cracking and distortion.
Flux-Cored Arc Welding (FCAW) for Cast Iron
- Choosing the Appropriate Flux-Cored Wire: Flux-cored wires with specialized iron-cast nickel cores are commonly used for FCAW on cast iron.
- Pre-Weld Preparations and Joint Designs: Proper joint designs and fit-up are crucial in FCAW to ensure proper penetration and fusion.
- Welding Process and Best Practices: Welders must use the correct settings and techniques to achieve good fusion and avoid defects.
- Post-Weld Inspections and Treatments: Inspecting the weld and applying post-weld treatments, such as stress relief, help improve the overall weld quality.
Tungsten Inert Gas Welding (TIG) for Cast Iron
- Gas Selection and Shielding Considerations: TIG welding on cast iron requires an inert gas, such as argon, to protect the weld zone from atmospheric contamination.
- Proper Setup and Equipment Requirements: TIG welding demands a clean welding environment and a precise tungsten electrode setup.
- Welding Techniques for Cast Iron: Proper manipulation of the torch and filler material is critical to achieve a strong, high-quality TIG weld on cast iron.
- Back Purging and Post-Weld Treatment: Back purging can be utilized to protect the backside of the weld from oxidation. Post-weld heat treatment may be necessary to improve ductility.
Post-Welding Considerations
Stress Relief and Annealing
After welding, cast iron components may undergo stress relief or annealing processes to reduce residual stresses and enhance the weld’s mechanical properties.
Machining and Finishing Operations
If required, machining and finishing operations can be performed on the welded components to achieve the desired final dimensions and surface characteristics.
Non-Destructive Testing (NDT) for Quality Assessment
Non-destructive testing techniques, such as ultrasonic testing or magnetic particle inspection, can be used to assess the integrity of the cast iron welds and detect any defects.
Common Welding Defects and Troubleshooting
Understanding Common Welding Defects in Cast Iron
Cast iron welding can be susceptible to various defects, which may include:
- Cracks: Due to the brittle nature of cast iron, improper cooling or high stresses during welding can lead to cracking.
- Porosity: Gas pockets trapped in the weld metal or heat-affected zone can result in porosity, weakening the weld.
- Incomplete fusion: Insufficient fusion between the weld metal and the base metal can compromise the weld’s strength.
- Distortion: Cast iron’s low thermal conductivity can cause significant distortion if not managed properly during welding.
Troubleshooting and Corrective Actions
To address these welding defects, the following corrective actions can be taken:
- Adjusting welding parameters: Modifying the heat input, travel speed, or current levels to achieve better fusion and reduce the likelihood of defects.
- Improving joint preparation: Proper beveling or joint design can promote better weld penetration and reduce the risk of incomplete fusion.
- Preheating optimization: Fine-tuning the preheating temperature and time can minimize thermal stresses and prevent cracking.
- Post-weld heat treatment: Stress-relieving the welded components can improve ductility and reduce residual stresses.
Prevention Strategies for Future Welds
Learning from previous welding defects is crucial in preventing them in future welds. Implementing robust quality control procedures, adhering to welding standards, and investing in proper training for welders can contribute to higher success rates in cast iron welding projects.
Safety and Environmental Concerns
Safety Precautions for Cast Iron Welding
Welders must prioritize safety by wearing appropriate personal protective equipment (PPE), such as welding helmets, gloves, and protective clothing, to shield against arc flash, sparks, and potential splatter.
Proper Ventilation and Fume Extraction
Adequate ventilation in the welding area is essential to disperse welding fumes and ensure a safe working environment. Welding on cast iron may produce harmful gases, such as carbon monoxide, which necessitates proper fume extraction systems.
Environmental Considerations for Waste Disposal
Responsible waste disposal practices should be adhered to, especially when dealing with welding byproducts. Ensuring proper handling and disposal of hazardous materials and adhering to environmental regulations is crucial.
Case Studies and Practical Applications
Real-Life Examples of Successful Cast Iron Welds
The inclusion of real-life examples of successful cast iron welds and their applications in various industries can provide insights into the effectiveness of different welding techniques.
Challenges Faced and Solutions Implemented
Analyzing challenges faced during past welding projects on cast iron and detailing the innovative solutions employed to overcome them offers valuable knowledge for future endeavors.
FAQs
What is cast iron, and why is welding it challenging?
Cast iron is an iron-carbon alloy with a higher carbon content than steel, giving it unique properties like high hardness and good wear resistance. Welding cast iron is challenging due to its brittle nature, susceptibility to cracking, and low ductility, requiring specific welding techniques to avoid defects.
Which welding processes are suitable for cast iron welding?
Several welding processes can be used for cast iron welding, including oxy-acetylene welding, shielded metal arc welding (SMAW), gas metal arc welding (GMAW/MIG), flux-cored arc welding (FCAW), and tungsten inert gas welding (TIG). Each process has its advantages and limitations, and the choice depends on factors such as joint design and thickness.
How can I prepare the cast iron part before welding?
Preparing the cast iron part is crucial for successful welding. Pre-cleaning the surface to remove impurities like grease, rust, and paint, ensuring proper fit-up and joint preparation, and selecting suitable filler materials are essential steps.
What are some common welding defects in cast iron, and how can they be addressed?
Common welding defects in cast iron include cracks, porosity, incomplete fusion, and distortion. To address these issues, welders can adjust welding parameters, improve joint preparation, optimize preheating procedures, and utilize post-weld heat treatment.
What safety precautions should I take when welding cast iron?
When welding cast iron, prioritize safety by wearing appropriate personal protective equipment (PPE), including welding helmets, gloves, and protective clothing. Ensure proper ventilation to disperse welding fumes and comply with environmental regulations for waste disposal.
How can I improve the longevity of cast iron welds?
To enhance the longevity of cast iron welds, implement stress relief or annealing post-welding, follow proper machining and finishing operations, and conduct non-destructive testing (NDT) for quality assessment.
Can you provide examples of successful cast iron welds in real-life applications?
Certainly! Case studies of successful cast iron welds, such as engine blocks, industrial machinery components, or automotive parts, showcase the effectiveness of various welding techniques in practical applications.
What role does welder training and certification play in cast iron welding?
Proper welder training and certification are essential for cast iron welding. Skilled and knowledgeable welders can select the right welding process, optimize parameters, and troubleshoot effectively, leading to high-quality welds and reduced rework or repairs.
Conclusion
In conclusion, mastering the welding techniques for cast iron is essential for achieving reliable, durable, and defect-free welds. Cast iron’s unique properties, including its high carbon content and brittleness, present challenges that demand careful consideration during the welding process. Throughout this article, we have explored various welding processes, such as oxy-acetylene welding, shielded metal arc welding (SMAW), gas metal arc welding (GMAW/MIG), flux-cored arc welding (FCAW), and tungsten inert gas welding (TIG), each with its benefits and limitations for cast iron applications.
Proper pre-welding preparations, such as cleaning, fit-up, and selection of appropriate filler materials, are crucial for ensuring successful welds. Additionally, post-weld heat treatment and stress relief techniques contribute to improved weld integrity and longevity. Understanding and addressing common welding defects, like cracks, porosity, incomplete fusion, and distortion, are key to enhancing weld quality and preventing costly repairs.
Welding safety and environmental considerations are paramount when working with cast iron, necessitating the use of suitable personal protective equipment (PPE) and proper ventilation to mitigate potential health and environmental hazards.