The Ultimate Showdown: Welding vs. Fastening – Which is Better?
Introduction
Joining techniques are essential in construction, manufacturing, and other industries that require the assembly of materials. The choice of joining technique can greatly affect the strength, durability, and overall quality of the final product. Welding and fastening are two of the most popular methods of joining materials, each with its own advantages and disadvantages.
Welding is a process of joining materials by melting them together using heat and pressure. It is a popular technique for creating strong and durable joints, and is suitable for a wide range of materials including metals, plastics, and composites. However, welding requires specialized equipment and training, and can be time-consuming and labor-intensive. It can also create deformation or distortion in the materials being joined, which may require additional processing steps to correct.
Fastening, on the other hand, involves joining materials by using mechanical means such as screws, bolts, rivets, or adhesives. It is a fast and easy way to join materials, and can be disassembled and reassembled easily. Fastening also requires minimal training and equipment, and is suitable for a range of materials including metals, wood, and plastics. However, fastening is not as strong or durable as welding, and may require additional hardware or components.
The purpose of this article is to compare the advantages and disadvantages of welding and fastening, and help readers determine which method is best for their project. By understanding the strengths and limitations of each technique, readers can make informed decisions about which joining method to use for achieving a successful and long-lasting result.
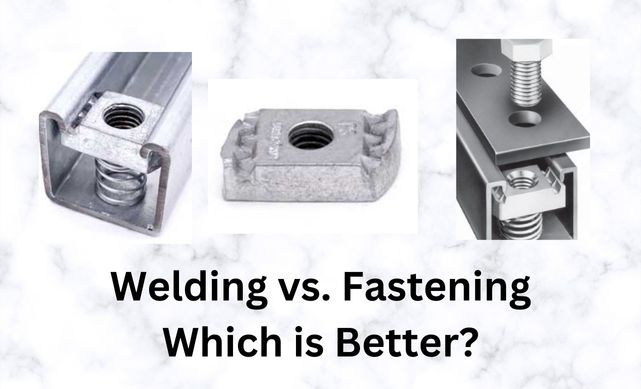
Welding
Definition and explanation of welding
Welding is a joining technique that involves melting and fusing materials together using heat and pressure. It is commonly used in construction, manufacturing, and other industries that require strong and durable joints between materials.
The welding process typically involves the use of a heat source, such as a flame or an electric arc, to melt the edges of the materials being joined. As the materials melt, they fuse together and solidify to form a strong bond. The type of heat source and welding technique used will depend on the specific materials being joined, as well as the desired strength and durability of the joint.
Advantages of welding
One of the primary advantages of welding is the strength and durability of the joint that is created. Welded joints are typically stronger than fastened joints because the materials being joined are fused together at the molecular level. This results in a joint that is less likely to fail or become weakened over time. Welding is also suitable for a wide range of materials, including metals, plastics, and composites.
Disadvantages of welding
However, welding also has some disadvantages. One of the main drawbacks is the specialized equipment and training required to perform the welding process. Welding typically requires the use of a welding machine, electrodes or filler material, and protective gear such as gloves, masks, and goggles. In addition, the welding process can be time-consuming and labor-intensive, which can result in higher production costs.
Another potential drawback of welding is that it can create deformation or distortion in the materials being joined. The heat from the welding process can cause the materials to warp, which may require additional processing steps to correct. Welding also produces hazardous fumes and gases, which can pose health risks to welders if proper safety measures are not taken.
In summary, welding is a powerful joining technique that can produce strong and durable joints between materials. However, it requires specialized equipment and training, and can be time-consuming and labor-intensive. The potential for distortion and the production of hazardous fumes must also be taken into account when considering the use of welding as a joining technique.
Fastening
Definition and explanation of fastening
Fastening is a joining technique that involves using mechanical means to secure materials together. This can be done using screws, bolts, nuts, rivets, or other types of hardware, as well as adhesives or other bonding agents. Fastening is a popular method for joining materials because it is fast and easy to install, and requires minimal training and equipment.
Fastening refers to the process of joining two or more objects or materials together by using mechanical means, such as screws, bolts, nuts, rivets, clips, or adhesives. Fastening is often used to create a temporary or semi-permanent joint between materials that may need to be taken apart or reassembled in the future. Fastening can be an effective joining technique when welding or other forms of fusion are not possible or desirable. Fasteners come in a variety of sizes, shapes, and materials, and the appropriate type and size of fastener must be selected based on the materials being joined and the specific application.
Advantages of fastening
One of the primary advantages of fastening is that it is quick and easy to install. Fasteners can be driven into place using a simple hand tool or power tool, which makes the process of joining materials much faster than welding. Additionally, fasteners can be easily disassembled and reassembled if needed, which makes them a good choice for applications that require periodic maintenance or repairs.
Another advantage of fastening is that it can be used with a variety of different materials, including metals, wood, and plastics. There are many different types of fasteners available, each designed to work with specific materials and applications. This makes fastening a versatile and flexible method for joining materials.
Disadvantages of fastening
However, fastening also has some disadvantages. One of the main drawbacks is that it is not as strong or durable as welding. Fasteners rely on the strength of the hardware or bonding agent being used, which can be less reliable than a fused joint created by welding. Additionally, the materials being joined may be weakened by the drilling or cutting required to install the fasteners.
Another potential drawback of fastening is that it may require additional hardware or components. For example, in order to install a bolt, a nut and washer may also be required. This can increase the cost and complexity of the joining process, especially if large numbers of fasteners are needed.
In summary, fastening is a quick and easy method for joining materials that requires minimal training and equipment. It is suitable for a variety of materials and applications, and can be easily disassembled and reassembled if needed. However, it may not be as strong or durable as welding, and may require additional hardware or components.
Comparison of welding and fastening
Strength and durability are two of the most important factors to consider. Welded joints are typically stronger and more durable than fastened joints, because the materials are fused together at the molecular level. This results in a joint that is less likely to fail or become weakened over time. On the other hand, fastened joints rely on the strength of the hardware or bonding agent being used, which can be less reliable than a fused joint created by welding.
Another factor to consider is the ease and speed of installation. Fastening is typically quicker and easier to install than welding, because it requires less specialized equipment and training. Fasteners can be driven into place using a simple hand tool or power tool, while welding requires a welding machine, electrodes or filler material, and protective gear such as gloves, masks, and goggles.
Cost is another important factor to consider. Welding can be more expensive than fastening because it requires more specialized equipment and training. However, welding may be more cost-effective in the long run, because welded joints are typically stronger and more durable, and require less maintenance and repair over time. Fastening may be more cost-effective in the short term, but may require more frequent maintenance or repairs.
The type of materials being joined is also an important factor to consider. Welding is suitable for a wide range of materials, including metals, plastics, and composites. Fastening may be less suitable for certain materials, or may require specialized fasteners or bonding agents.
Finally, safety is an important factor to consider when choosing between welding and fastening. Welding produces hazardous fumes and gases, which can pose health risks to welders if proper safety measures are not taken. Fastening does not produce hazardous fumes or gases, but may pose other safety risks if the hardware or bonding agent is not properly installed or maintained.
Welding vs. Fastening – Which is Better?
Welding and fastening are two methods of joining materials together. Welding is a permanent joining method that uses heat and pressure to melt and fuse materials. It creates a very strong and durable joint, but it can be more difficult and time-consuming than fastening. Fastening, on the other hand, uses mechanical force or adhesives to hold materials together. It is generally faster and easier than welding but may not provide as strong a joint. The choice between welding and fastening depends on the specific application, materials being joined, and the desired strength and durability of the joint.
Both welding and fastening have their advantages and disadvantages, and the best choice will depend on the specific application and requirements. Welding is typically stronger and more durable, but requires more specialized equipment and training. Fastening is quicker and easier to install, but may be less reliable and require more frequent maintenance or repairs. The type of materials being joined, cost, and safety are also important factors to consider when choosing between these two joining techniques.
Safety Concerns for Welding vs Fastening
Both welding and fastening have their own unique safety concerns that should be considered when selecting the appropriate joining technique for a specific application.
Safety Concerns for Welding
- Fire Hazard: Welding involves the use of heat, which can create sparks and ignite flammable materials, posing a fire hazard. Welding should always be performed in a well-ventilated area and with proper safety equipment.
- Fumes and Gases: Welding can produce hazardous fumes and gases that can pose a risk to the health and safety of workers. Welding should always be performed in a well-ventilated area and with appropriate respiratory protection.
- Structural Integrity: Welding can create a strong and durable joint, but if not performed correctly, it can weaken the structural integrity of the materials being joined, leading to potential failures or collapse.
Safety Concerns for Fastening
- Loosening: Fasteners can become loose over time due to vibration or other forces, leading to potential failures or collapse. It is important to use the appropriate type and size of fasteners for the specific application and to follow proper installation procedures.
- Corrosion: Fasteners can corrode over time due to exposure to the elements or chemicals, leading to potential failures or collapse. It is important to use the appropriate type of fasteners for the specific environment and to follow proper maintenance procedures.
- Tampering: Fasteners can be easily tampered with or removed, making them less secure than welded joints. It is important to use the appropriate type and number of fasteners for the specific application and to follow proper security procedures.
FAQs
Is welding stronger than fasteners?
Yes, welding is typically stronger than fasteners because the materials are fused together at the molecular level, creating a joint that is less likely to fail or become weakened over time. Fasteners, on the other hand, rely on the strength of the hardware or bonding agent being used, which can be less reliable than a fused joint created by welding.
What is welding in fastening?
Welding is a technique used to join materials together by using heat and pressure to fuse them together at the molecular level. It is a type of fastening that creates a strong and durable joint by melting and fusing the materials together.
What is the difference between welding and bolting?
Welding involves using heat and pressure to fuse materials together, while bolting involves using mechanical means to secure materials together using bolts, nuts, and washers. Welding typically creates a stronger and more durable joint, but requires specialized equipment and training, while bolting is quicker and easier to install but may be less reliable.
Why welding is a better joining technique than mechanical fasteners?
Welding is often considered a better joining technique than mechanical fasteners because it creates a stronger and more durable joint that is less likely to fail or become weakened over time. Welded joints are also typically more resistant to corrosion and can withstand extreme temperatures and stress. However, welding requires more specialized equipment and training, and can be more expensive than mechanical fastening.
Is welding better than riveting?
Whether welding is better than riveting depends on the specific application and requirements. Welding typically creates a stronger and more durable joint than riveting, but it also requires more specialized equipment and training. Riveting, on the other hand, is quicker and easier to install and may be more suitable for certain applications.
What are the disadvantages of welding over bolting?
The disadvantages of welding over bolting include the fact that welding requires more specialized equipment and training, can be more expensive, and can create hazardous fumes and gases that pose health risks to workers if proper safety measures are not taken. Bolting, on the other hand, may be less reliable and may require more frequent maintenance or repairs.
What is called welding?
Welding is a joining technique that involves using heat and pressure to fuse materials together at the molecular level, creating a strong and durable joint. There are several types of welding, including arc welding, gas welding, and resistance welding, among others.
What are types of fastening?
There are several types of fastening, including mechanical fastening, which uses hardware such as bolts, screws, and rivets to secure materials together, as well as adhesive fastening, which uses bonding agents to join materials together.
Why is fastening used?
Fastening is used to join materials together in a variety of applications, including construction, manufacturing, and automotive industries. It is a quick and easy way to secure materials together and can be more cost-effective than other joining techniques, such as welding. Fastening can also be less hazardous than welding, as it does not produce hazardous fumes or gases.
Conclusion
In conclusion, both welding and fastening are popular techniques for joining materials together. Welding is a method that uses heat and pressure to fuse materials together, creating a strong and durable joint. Fastening, on the other hand, involves using mechanical means to secure materials together, which is quick and easy to install but may be less reliable.
When choosing between these two methods, it’s important to consider factors such as the strength and durability required, the ease and speed of installation, the cost, and the type of materials being joined. Ultimately, the best choice will depend on the specific application and requirements.
Whether it’s welding or fastening, it’s important to follow proper safety measures to ensure the safety of the workers and the quality of the joint. Proper training, equipment, and maintenance are essential to creating a strong and reliable joint that will stand the test of time.