What Is Inertia Welding?
Inertia welding, also known as rotary friction welding or flywheel welding, is a solid-state welding process that joins two metal workpieces through the application of rotational and axial forces. It utilizes the principle of generating frictional heat at the joint interface to create a metallurgical bond between the materials. Unlike traditional fusion welding methods that involve melting and solidification, inertia welding achieves welding without melting the workpieces.
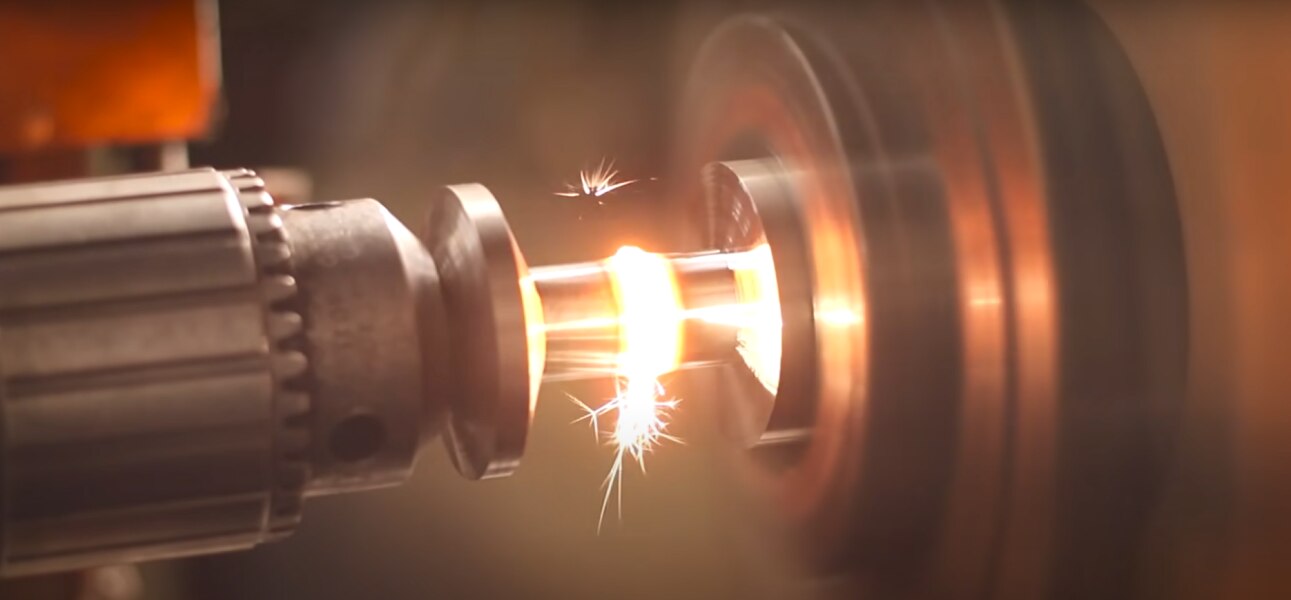
Brief overview of its applications and advantages
Inertia welding has gained recognition for its various applications across multiple industries. Some of the notable advantages and applications include:
- Automotive Industry: Inertia welding is widely used in the automotive sector for joining various components, such as engine crankshafts, drive shafts, and suspension parts. The process enables the production of high-strength, durable, and cost-effective welds that meet stringent performance requirements.
- Aerospace and Aviation Sector: Inertia welding finds application in the aerospace industry for joining critical components, including turbine discs, fan blades, and aircraft landing gear parts. The process offers excellent weld quality, ensuring structural integrity and reliability in demanding operating conditions.
- Oil and Gas Industry: Inertia welding plays a crucial role in the oil and gas sector for fabricating drill pipes, drill collars, and other downhole tools. The high-strength welds produced through inertia welding contribute to enhanced performance, extended service life, and improved operational efficiency in harsh environments.
- Power Generation and Turbine Manufacturing: Inertia welding is employed in the production of steam and gas turbine components, such as rotor shafts, blades, and vanes. The process ensures the integrity and durability of the welds, contributing to the overall efficiency and reliability of power generation systems.
- Other Industrial Sectors: Inertia welding has applications in various other industries, including heavy machinery manufacturing, railway systems, shipbuilding, and renewable energy sectors. Its advantages, such as superior joint strength, efficient use of energy, and the ability to join dissimilar materials, make it a preferred choice for specific welding requirements.
The process of inertia welding offers several advantages over conventional fusion welding methods:
- Strong metallurgical bond: Inertia welding produces high-quality welds with a metallurgical bond, resulting in joint strength comparable to or exceeding the base material.
- Energy efficiency: As it is a solid-state welding process, inertia welding consumes significantly less energy compared to fusion welding methods, leading to cost savings and reduced environmental impact.
- Joining dissimilar materials: Inertia welding facilitates the joining of different materials, including dissimilar metals, allowing the combination of desired properties and compatibility for specific applications.
- Time and cost-effective: The process is relatively fast and automated, enabling efficient production rates, reduced labor costs, and improved overall productivity.
- Reduced distortion and heat-affected zone (HAZ): Inertia welding minimizes distortion and the size of the HAZ, preserving the mechanical properties and integrity of the workpieces.
These advantages make inertia welding an attractive choice for various industries seeking reliable and efficient joining solutions.
Principle of Inertia Welding
Explanation of the basic principle
Inertia welding operates on the principle of generating frictional heat at the joint interface to create a metallurgical bond between two metal workpieces. The process involves the application of rotational and axial forces to produce relative motion between the two components.
The basic steps of inertia welding are as follows:
- The two workpieces to be welded are securely clamped into the welding machine.
- One workpiece, called the “driver,” is attached to a rotating spindle, while the other workpiece, called the “driven,” remains stationary.
- The rotational motion of the driver workpiece generates frictional heat at the joint interface.
- As the heat is generated, the driver workpiece transfers energy to the driven workpiece, causing it to reach a plasticized state near the interface.
- Once the desired temperature is achieved, the rotational motion of the driver is stopped, and axial pressure is applied to forge the softened material of the driven workpiece.
- The axial pressure forces the softened material to flow, creating plastic deformation and forming a solid-state metallurgical bond between the workpieces.
- After the forging phase, the weld is allowed to cool down and solidify, resulting in a strong and reliable joint.
Description of the equipment and components used
Inertia welding requires specialized equipment designed to facilitate the process. The main components typically include:
- Machine Structure: The machine structure provides a stable foundation and rigidity to withstand the forces generated during the welding process. It consists of a solid base, columns, and supports for holding the workpieces securely in place.
- Spindle and Chuck Assembly: The spindle is responsible for rotating the driver workpiece, and it is driven by an electric motor or other suitable power source. The chuck assembly securely holds the driver workpiece and ensures proper alignment and stability during rotation.
- Clamping Mechanism: The clamping mechanism is used to firmly hold the workpieces in position during the welding process. It ensures that the joint interface remains aligned and allows for the transfer of forces without slippage.
- Axial Cylinder: An axial cylinder is employed to apply axial pressure to the driven workpiece during the forging phase. It exerts controlled force to facilitate plastic deformation and the formation of a solid-state weld.
- Control System: A control system comprising sensors, actuators, and a programmable logic controller (PLC) regulates and monitors various parameters such as rotational speed, axial pressure, and welding time. It ensures precise control over the welding process to achieve desired weld quality and consistency.
Role of rotational and axial forces in the process
The rotational and axial forces are integral to the success of inertia welding:
- Rotational Force: The rotational force applied to the driver workpiece generates friction at the joint interface. This frictional heat softens the material, preparing it for plastic deformation and bonding. The rotational speed influences the amount of heat generated and must be optimized for each specific welding application.
- Axial Force: The axial force is applied to the workpieces during the forging phase, following the heating phase. It facilitates the plastic flow and deformation of the softened material, allowing for the formation of a solid-state weld. The axial force must be carefully controlled to ensure sufficient pressure for bonding without causing excessive deformation or material damage.
Together, these forces, combined with the controlled heating and forging phases, enable the successful formation of a strong, metallurgical bond between the workpieces in inertia welding. The precise control and coordination of these forces are essential for achieving high-quality and reliable welds.
Process Steps
Pre-welding Preparation
- Selection of suitable materials for inertia welding: Before the welding process, it is crucial to choose compatible materials that can form a strong metallurgical bond through inertia welding. The materials should have similar thermal and mechanical properties to ensure successful joining.
- Machining and cleaning of workpieces: The workpieces undergo machining processes to achieve precise dimensions and clean surfaces. This involves turning, milling, or other machining techniques to remove any surface contaminants, oxides, or coatings that may hinder the welding process.
- Fixturing and alignment of the components: The workpieces are securely positioned and aligned using specialized fixtures or clamps. Proper alignment ensures that the joint interface is in contact and properly positioned to enable efficient energy transfer during the welding process.
Heating Phase
- Activation of the equipment and setup of welding parameters: The welding machine is activated, and the necessary parameters are set. This includes selecting the appropriate rotational speed, axial force, and welding time based on the specific materials, joint design, and desired weld quality.
- Introduction of rotational and axial forces: The rotational force is applied to the driver workpiece using the spindle, initiating the relative motion between the workpieces. Simultaneously, the axial force is gradually applied to the driven workpiece using the axial cylinder. These forces work in conjunction to facilitate the welding process.
- Generation of frictional heat at the joint interface: As the driver workpiece rotates, it generates frictional heat at the joint interface due to the contact and relative motion with the driven workpiece. This frictional heat softens the material and raises the temperature at the joint interface, preparing it for plastic deformation and bonding.
Forging Phase
- Transition from heating to forging phase: Once the desired temperature is reached, the rotational motion of the driver workpiece is stopped. The heating phase transitions into the forging phase, where the focus shifts from generating heat to applying axial pressure and creating plastic deformation.
- Application of higher axial pressure to forge the joint: The axial force is increased to a predetermined level, exerting pressure on the softened material. This pressure causes the material to flow and deform plastically, ensuring intimate contact and intermixing of the atoms at the joint interface.
- Plastic deformation and metallurgical bonding of the materials: Under the applied pressure, the softened material undergoes plastic deformation, filling any gaps or voids at the joint interface. The material flows and interdiffuses, resulting in metallurgical bonding between the workpieces. As the pressure continues, the material solidifies, forming a strong, solid-state weld.
Cooling and Post-welding
- Termination of heating and forging forces: After the desired forging time, the axial pressure is gradually released, and the rotational motion of the driver workpiece is halted. The heat input is discontinued, allowing the weld area to cool down.
- Natural or controlled cooling of the welded joint: The welded joint is allowed to cool naturally or through controlled cooling methods, depending on the specific materials and requirements. Proper cooling ensures the formation of a desirable microstructure and the prevention of excessive residual stresses.
- Inspection, testing, and post-weld processing if required: The welded joint undergoes inspection and testing to ensure its quality and integrity. Non-destructive testing methods, such as visual inspection, ultrasonic testing, or radiographic examination, may be employed. Post-weld processing, such as machining or surface finishing, may be performed to meet dimensional or aesthetic requirements.
Advantages and Limitations
Advantages of Inertia Welding
- High quality and strength of the welded joint: Inertia welding produces high-quality welds with a metallurgical bond, resulting in joints that exhibit strength comparable to or exceeding the base materials. The absence of fusion and solidification ensures minimal defects, such as porosity or cracking, leading to reliable and structurally sound welds.
- Efficient use of energy and minimal heat input: Inertia welding is an energy-efficient process since it does not rely on melting the workpieces. The generation of frictional heat at the joint interface and the subsequent plastic deformation require significantly less energy compared to fusion welding methods. This energy efficiency translates into cost savings and reduced environmental impact.
- Versatility in joining dissimilar materials: Inertia welding allows the joining of dissimilar materials, including different metals or even combinations of metal and non-metal materials. This versatility enables the creation of hybrid structures that combine desired properties from multiple materials, such as strength, corrosion resistance, or heat resistance.
Limitations and Considerations
- Size and geometry restrictions of workpieces: Inertia welding is typically suitable for relatively small to medium-sized workpieces due to the limitations of available equipment and the forces involved. Large or bulky components may be challenging to accommodate in the welding machine and may require specialized setups.
- Material compatibility and weldability: The success of inertia welding depends on the compatibility and weldability of the materials being joined. The materials should have similar thermal and mechanical properties to ensure effective energy transfer and plastic deformation. Some materials may exhibit poor weldability due to factors such as composition, microstructure, or surface conditions.
- Cost and complexity of the equipment: Inertia welding requires specialized equipment, including the welding machine, spindle, chuck assembly, and control system. The initial investment and maintenance costs associated with this equipment can be relatively high. Additionally, the complexity of the equipment setup and operation may require skilled operators and technicians.
Applications of Inertia Welding
Automotive industry
Inertia welding finds extensive use in the automotive sector for joining various components that require high strength and durability. Some specific applications include:
- Engine crankshafts: Inertia welding is used to join the main journal and connecting rod journal to create a robust and balanced crankshaft.
- Drive shafts: Inertia welding is employed to join drive shaft segments, ensuring seamless power transmission and improving overall efficiency.
- Suspension parts: Components such as control arms, stabilizer bars, and steering linkages benefit from the high-quality welds achieved through inertia welding.
Aerospace and aviation sector
Inertia welding plays a vital role in the aerospace and aviation industry, where the demand for lightweight, high-strength, and reliable components is critical. Some key applications include:
- Turbine discs and blades: Inertia welding is used to join the individual blades to the rotor disc, ensuring high structural integrity and performance.
- Fan blades: Inertia welding joins the blades to the hub, creating a strong and balanced fan assembly for efficient airflow in aircraft engines.
- Landing gear components: Various parts of landing gear, such as struts, pistons, and linkages, are joined through inertia welding to withstand the demanding operating conditions.
Oil and gas industry
The oil and gas sector relies on inertia welding for the fabrication of equipment and components used in exploration, drilling, and production. Some notable applications include:
- Drill pipes and collars: Inertia welding is used to join the sections of drill pipes and collars, ensuring strength, integrity, and reliability in harsh drilling environments.
- Downhole tools: Components like stabilizers, reamers, and subs are inertia-welded to withstand the extreme conditions encountered in oil and gas wells.
- Pipeline connectors: Inertia welding is employed to create reliable welds between pipeline sections, providing efficient flow and structural integrity.
Power generation and turbine manufacturing
Inertia welding plays a crucial role in the power generation industry, particularly in turbine manufacturing. Some significant applications include:
- Rotor shafts: Inertia welding joins rotor shaft segments to form a single, high-strength shaft for steam and gas turbines, ensuring reliable power generation.
- Turbine blades and vanes: Inertia welding joins individual blades or vanes to the turbine rotor, ensuring optimal aerodynamic performance and longevity.
- Heat exchanger components: Inertia welding is used to join various parts of heat exchangers, such as tube sheets and tubes, ensuring efficient heat transfer and structural integrity.
Other industrial sectors
Inertia welding has applications in various other industrial sectors, including:
- Heavy machinery manufacturing: Inertia welding joins components of heavy machinery, such as excavator booms, crane structures, and agricultural equipment, providing robust and durable connections.
- Railway systems: Inertia welding is used in the manufacturing of railway components, such as axles, couplings, and suspension parts, ensuring reliable and safe operation.
- Renewable energy sectors: Components for wind turbines, such as tower sections and blade connectors, can be joined using inertia welding for enhanced performance and longevity.
FAQs
What is inertia welding used for?
Inertia welding is used for joining metal workpieces in various industries, including automotive, aerospace, oil and gas, power generation, and more.
What is inertia welding a form of?
Inertia welding is a form of solid-state welding, where the joint is formed without melting the workpieces.
What is the difference between friction and inertia welding?
The difference lies in the mechanism of heat generation. In friction welding, heat is generated by rubbing the workpieces together, while in inertia welding, heat is generated by the relative rotational motion between the workpieces.
Is inertia welding a modified form of friction welding?
Yes, inertia welding can be considered a modified form of friction welding, where the rotational force is used to generate heat and achieve the desired weld.
What are the benefits of inertia welding?
The benefits of inertia welding include high-quality and strong welded joints, energy efficiency, versatility in joining dissimilar materials, and reduced distortion and heat-affected zone.
What is the strongest welding process?
The strength of a weld depends on various factors, including the materials being welded and the welding technique employed. However, processes like electron beam welding and laser welding are known for producing high-strength welds.
What is inertia called?
Inertia is the property of matter that resists changes in its state of motion or rest.
What are two types of inertia?
The two types of inertia are:
- Mass inertia (also called translational inertia) – the resistance to changes in linear motion.
- Moment of inertia (also called rotational inertia) – the resistance to changes in rotational motion.
What is inertia type?
Inertia can refer to different types depending on the context. In the context of welding, “inertia” generally refers to inertia welding, which is a specific welding process that joins metal workpieces through rotational and axial forces.
Conclusion
Inertia welding, also known as rotary friction welding or flywheel welding, is a solid-state welding process that joins two metal workpieces through the application of rotational and axial forces. The basic principle involves generating frictional heat at the joint interface to create a metallurgical bond. The process steps include pre-welding preparation, heating phase, forging phase, and cooling/post-welding.
Inertia welding offers several advantages, including high-quality and strong welded joints, efficient use of energy with minimal heat input, and the ability to join dissimilar materials. These benefits make it suitable for various industries and applications. In the automotive sector, it is used for components such as crankshafts, drive shafts, and suspension parts. In the aerospace industry, it is employed for turbine discs, fan blades, and landing gear components. The oil and gas industry utilizes inertia welding for drill pipes, downhole tools, and pipeline connectors. Power generation and turbine manufacturing sectors benefit from inertia welding for rotor shafts, turbine blades, and heat exchanger components. Additionally, inertia welding finds application in other industrial sectors such as heavy machinery manufacturing, railway systems, and renewable energy sectors.
Inertia welding continues to evolve with advancements in equipment technology and materials. The development of more sophisticated control systems and automation has increased the precision and reliability of the process. Research and development efforts are focused on expanding the range of materials that can be inertia-welded, including advanced alloys and composite materials. Additionally, ongoing advancements in process monitoring and non-destructive testing techniques are expected to further enhance the quality assurance of inertia welds. As industries continue to seek efficient, reliable, and cost-effective joining methods, the future of inertia welding looks promising, with potential applications in emerging sectors and the potential for further optimization and advancements in the field.