Introduction
Plug welding is a widely used technique in the realm of metal fabrication and welding. It involves joining two metal pieces together by filling a hole in one of the pieces with molten metal. This creates a secure and strong bond between the two pieces, akin to traditional spot welding but with a slightly different approach. Understanding the process of plug welding is crucial for anyone involved in metalworking or fabrication, as it offers several advantages over other welding methods and can be applied across various industries.
Understanding the Plug Welding Process
Definition and Explanation of Plug Welding
Plug welding is a welding technique used to join two metal pieces together by filling a hole in one of the pieces with molten metal. This creates a strong and permanent bond between the two pieces, similar to spot welding but with a different approach. The process is commonly employed in various industries such as automotive, manufacturing, construction, and aerospace.
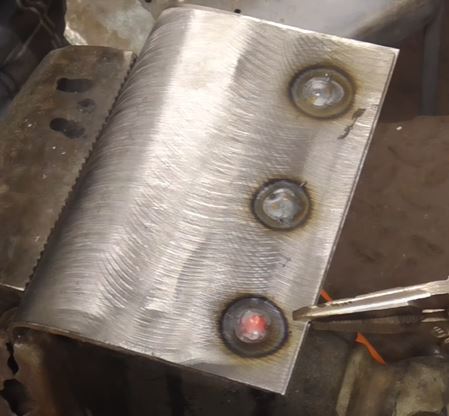
Step-by-Step Guide to Executing a Plug Weld
- Preparation of Materials: Before beginning the plug welding process, it’s essential to prepare the materials properly. This includes ensuring that the metal pieces to be welded are clean, free from any contaminants such as rust or paint, and properly aligned for welding.
- Drilling or Punching the Hole: The next step involves drilling or punching a hole in one of the metal pieces. The size and placement of the hole are crucial and should be in accordance with the welding specifications and requirements.
- Fitting the Pieces Together: Once the hole is created, the two metal pieces are fitted together, ensuring that they are properly aligned and in contact with each other. This step is essential for achieving a strong and reliable weld.
- Welding Process: With the pieces properly aligned and in place, the welding process can commence. An electric arc or other heat source is used to melt the filler metal, which is then deposited into the hole, forming the weld. The welding electrode is typically inserted into the hole to facilitate the welding process.
Importance of Proper Technique and Equipment
Proper technique and equipment are crucial for successful plug welding:
- Technique: The welder must have a good understanding of welding fundamentals and techniques to ensure proper penetration and fusion of the weld. This includes maintaining the correct welding parameters, such as heat input and travel speed, throughout the welding process.
- Equipment: Using the right welding equipment and tools is essential for achieving quality plug welds. This includes selecting the appropriate welding machine, electrodes, and protective gear. Additionally, ensuring that the welding equipment is properly maintained and calibrated is important for consistent and reliable weld quality.
Common Mistakes in Plug Welding
Lack of Proper Surface Preparation
One of the most common mistakes in plug welding is the failure to adequately prepare the surfaces of the metal pieces to be welded. This can include neglecting to remove rust, paint, or other contaminants from the welding area. Improper surface preparation can lead to poor weld quality, including weak bonds and increased susceptibility to corrosion.
Incorrect Hole Size or Placement
Another common mistake is drilling or punching holes that are either too small or too large, or placing them in the wrong location. This can result in improper fit-up between the metal pieces and compromised weld strength. It’s crucial to carefully follow welding specifications and guidelines regarding hole size, placement, and spacing to ensure proper weld quality.
Inadequate Penetration or Fusion
Insufficient penetration or fusion of the weld is a common issue in plug welding, often resulting from improper welding parameters or technique. Inadequate penetration can weaken the weld joint and compromise its structural integrity. Welders must ensure that the welding parameters, such as current, voltage, and travel speed, are properly adjusted to achieve adequate penetration and fusion.
Overheating or Burn-Through
Overheating or burn-through occurs when the welding heat input is too high, leading to excessive melting of the base metal and the formation of holes or gaps in the weld. This can weaken the weld joint and cause distortion or warping of the metal pieces. Proper control of welding parameters, such as heat input and travel speed, is essential for preventing overheating and burn-through.
Solutions and Tips for Avoiding These Mistakes
To avoid these common mistakes in plug welding, consider the following solutions and tips:
- Thoroughly clean and prepare the welding surfaces before welding to ensure proper adhesion and bond strength.
- Follow welding specifications and guidelines regarding hole size, placement, and spacing.
- Use proper welding technique and parameters to achieve adequate penetration and fusion of the weld.
- Monitor welding heat input and adjust parameters as needed to prevent overheating and burn-through.
- Conduct regular inspections and quality checks throughout the welding process to identify and address any issues promptly.
Advantages and Disadvantages of Plug Welding
Advantages
- Strong and Durable Welds: Plug welding creates robust and long-lasting welds, ensuring the structural integrity and reliability of the joined components or structures.
- Minimal Distortion and Warping: Compared to some other welding techniques, plug welding often results in less distortion and warping of the metal pieces, particularly when welding thin materials.
- Suitable for a Variety of Materials and Thicknesses: Plug welding can be used to join a wide range of materials, including steel, aluminum, and stainless steel, as well as varying thicknesses of metal sheets or plates.
- Cost-Effective and Efficient: Plug welding is a cost-effective and efficient welding method, as it requires minimal material and equipment and can be performed relatively quickly compared to other welding techniques.
- Enhanced Aesthetics and Finishing Options: Plug welding offers enhanced aesthetics and finishing options, as it creates cleaner and more seamless weld joints, making it suitable for applications where appearance is important.
Disadvantages
- Limited Access for Welding in Tight Spaces: Plug welding may be challenging or impractical in situations where access to the welding area is limited, such as tight corners or confined spaces.
- Requires Precise Alignment and Fit-Up: Achieving proper alignment and fit-up between the metal pieces is crucial for successful plug welding, requiring careful preparation and attention to detail.
- Potential for Weld Inconsistency if Not Executed Properly: Improper execution of plug welding can result in inconsistent welds, leading to weak joints and compromised structural integrity.
- Not Suitable for All Applications or Materials: While plug welding is versatile, it may not be suitable for all welding applications or materials, particularly in cases where high-strength or specialized welding techniques are required.
Uses and Applications of Plug Welding
Automotive Industry
In the automotive industry, plug welding is commonly used for various applications, including car body assembly. It allows manufacturers to join different metal components securely, contributing to the structural integrity and safety of vehicles. Plug welding is often utilized in the assembly of chassis components, body panels, frames, and other structural elements of automobiles.
Manufacturing of Appliances and Furniture
Plug welding finds extensive applications in the manufacturing of appliances and furniture. It enables manufacturers to join metal components efficiently and securely, contributing to the durability and longevity of products. In appliance manufacturing, plug welding is used for assembling components such as cabinets, frames, and internal structures. Similarly, in furniture manufacturing, plug welding is employed for joining metal parts of chairs, tables, cabinets, and other furniture items.
Construction and Structural Applications
In the construction industry, plug welding is utilized for various structural applications, particularly in steel and metal construction projects. It allows construction professionals to join structural steel components securely, such as beams, columns, trusses, and other load-bearing elements. Plug welding plays a crucial role in ensuring the stability, strength, and integrity of buildings, bridges, industrial facilities, and other structures.
Shipbuilding and Marine Industry
Plug welding is extensively used in the shipbuilding and marine industry for joining metal components of ships, boats, and marine structures. It enables shipbuilders to create strong and watertight welds, contributing to the seaworthiness and durability of vessels. Plug welding is employed in the assembly of hulls, decks, bulkheads, superstructures, and other components of ships and boats, ensuring their structural integrity and performance in harsh marine environments.
Aerospace and Aviation Applications
In the aerospace and aviation industry, plug welding is employed for various critical applications, particularly in the fabrication and assembly of aircraft and spacecraft structures. It allows aerospace engineers to join lightweight yet high-strength materials, such as aluminum and titanium alloys, with precision and reliability. Plug welding is utilized in the assembly of aircraft fuselages, wings, empennage, engine components, and other structural elements, contributing to the safety, performance, and efficiency of aerospace vehicles.
FAQs
What materials can be joined using plug welds?
Plug welding can be performed on a wide range of materials, including steel, aluminum, stainless steel, and other metals commonly used in manufacturing and construction.
Is plug welding suitable for structural applications?
While plug welding can provide strong and durable joints, its suitability for structural applications depends on factors such as material thickness, joint design, and load requirements. Engineers should carefully evaluate the specific needs of their project before selecting welding methods.
Can plug welds be performed using different welding techniques?
Yes, plug welds can be performed using various welding techniques, including MIG welding, TIG welding, and spot welding. The choice of technique depends on factors such as material type, thickness, and accessibility.
How can one determine the appropriate plug weld size?
The size of the plug weld hole should be determined based on factors such as material thickness, joint design, and welding technique. Welding standards and guidelines provide recommendations for hole size based on these factors.
Are there any alternatives to plug welding for joining metal components?
Yes, there are several alternatives to plug welding, including riveting, adhesive bonding, soldering, and brazing. The choice of joining method depends on factors such as material properties, joint design, and application requirements.
Conclusion
Plug welding is a valuable welding technique with diverse applications and benefits across industries. By mastering plug welding and continually exploring its possibilities, professionals can unlock opportunities for personal and professional growth while contributing to the advancement and success of their respective industries.