What is Welding?
Introduction
Welding is a process of joining two or more pieces of metal or thermoplastics together using heat and/or pressure. It is a crucial technology that has revolutionized various industries such as manufacturing, construction, automotive, aerospace, and more. Welding is essential in creating sturdy and durable products that can withstand high stress, heat, and pressure.
The origins of welding can be traced back to the Bronze Age when blacksmiths used heat to fuse metals together. However, it was not until the 19th century that welding became an important industrial process with the introduction of the electric arc welding method. Since then, welding has continued to evolve with advancements in technology and materials.
Today, welding plays a vital role in many industries, such as shipbuilding, oil and gas, aerospace, automotive, and construction. Welding is used in creating everything from pipelines, bridges, and skyscrapers to cars, airplanes, and satellites.
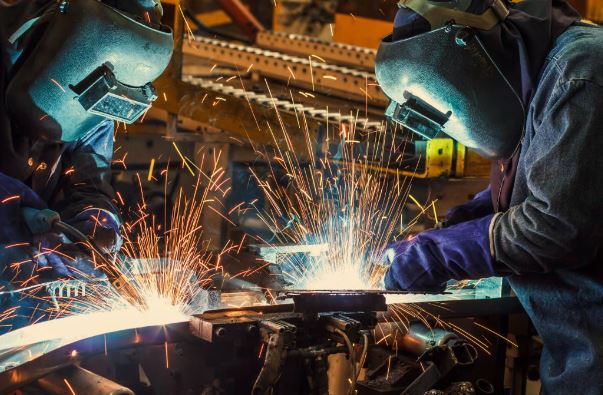
Types of Welding
There are several types of welding techniques, each with its unique characteristics and advantages. Here are some of the most commonly used types of welding:
Arc welding:
Arc welding is a method of welding that uses an electric arc between an electrode and the base material to melt the metal and create a bond. This type of welding can be further divided into several subcategories, such as shielded metal arc welding (SMAW), gas metal arc welding (GMAW), flux-cored arc welding (FCAW), and more.
Gas welding:
Gas welding is a welding process that uses a gas flame to melt the metal and join it together. The most common types of gas welding are oxy-fuel welding and oxy-acetylene welding. Gas welding is commonly used in plumbing, HVAC, and metalworking applications.
Resistance welding:
Resistance welding is a type of welding that uses electric current to join two metals together. The metals are held between two electrodes, and a current is passed through them, melting the metals and creating a bond. Spot welding and seam welding are two common types of resistance welding.
Laser welding:
Laser welding is a high-precision welding process that uses a laser beam to join metals together. This type of welding is commonly used in the aerospace and medical industries for its accuracy and precision.
Other types of welding:
There are several other types of welding techniques, including electron beam welding, friction stir welding, ultrasonic welding, and more. Each of these techniques has its unique characteristics and applications.
Welding Processes
Welding is a complex process that involves several steps and considerations to achieve a successful weld. Here are some of the key processes involved in welding:
Preparation for welding:
The first step in welding is preparing the metal surfaces to be joined. This includes cleaning, degreasing, and removing any rust, paint, or other contaminants that could affect the quality of the weld. The metal surfaces should also be properly aligned and held in place to ensure that the weld is strong and secure.
Joint design:
The design of the joint to be welded is critical to the success of the weld. The joint should be designed to ensure that the weld is strong and able to withstand the intended use and load. Factors such as the type of joint, the thickness of the metal, and the welding position all play a role in joint design.
Filler material selection:
In most welding processes, filler material is used to fill the gap between the two metal surfaces being joined. The filler material must be compatible with the base material and be able to withstand the intended use and load.
Welding techniques:
There are several welding techniques available, each with its unique advantages and disadvantages. The welding technique used will depend on the type of joint, the metal being joined, and the desired quality of the weld. Some common welding techniques include MIG welding, TIG welding, and stick welding.
Quality control and inspection:
Quality control and inspection are critical steps in the welding process to ensure that the weld is of high quality and meets the intended use and load. Visual inspection, x-ray testing, and ultrasonic testing are all common methods used to inspect welds and ensure their quality.
Welding Materials
Welding materials are the base metals and filler metals used in welding. Here are some of the key aspects of welding materials:
Common welding materials: The most commonly used welding materials include steel, aluminum, stainless steel, and copper alloys. Each of these materials has its unique properties and challenges when it comes to welding.
Properties of welding materials: The properties of welding materials, such as strength, ductility, and corrosion resistance, play a significant role in the welding process. The welding process must be chosen based on the properties of the materials being welded.
Challenges with welding different materials together: Welding dissimilar materials, such as steel and aluminum, can be challenging due to their different thermal conductivity and expansion rates. This can cause warping, cracking, and other defects in the weld.
Techniques for welding dissimilar materials: There are several techniques for welding dissimilar materials, including using intermediate materials, such as transition joints or filler metals, to join the materials. Other techniques include explosive welding, friction welding, and diffusion bonding.
Applications of Welding
Welding has numerous applications across various industries. Some of the most significant applications of welding include:
Automotive industry: Welding is a critical process in the automotive industry, where it is used to join various metal components such as frames, panels, and exhaust systems.
Construction industry: Welding plays an essential role in the construction industry, where it is used to join steel beams and columns, reinforce concrete structures, and install pipelines.
Manufacturing industry: Welding is used extensively in the manufacturing industry, where it is used to join metal components in the production of machinery, equipment, and tools.
Aerospace industry: Welding is widely used in the aerospace industry, where it is used to manufacture aircraft components such as wings, fuselage, and landing gear.
Other industries: Welding is also used in various other industries such as shipbuilding, railroads, power plants, and oil and gas refineries.
Future of Welding
Welding technology has evolved over the years, and new advancements are emerging to make welding processes more efficient and effective. Here are some of the key aspects of the future of welding:
Advancements in welding technology: New welding technologies, such as friction stir welding, laser welding, and electron beam welding, are emerging to make welding faster, cleaner, and more precise.
Automation of welding processes: Automation is increasingly being used in welding processes, leading to increased efficiency, accuracy, and safety. Robotic welding systems are becoming more prevalent, and new developments in artificial intelligence and machine learning are improving the capabilities of welding robots.
Impact of Industry 4.0 on welding: Industry 4.0, the fourth industrial revolution, is transforming the manufacturing industry with the integration of advanced technologies, such as the Internet of Things, big data analytics, and cloud computing. Welding is also being impacted by Industry 4.0, with the emergence of smart welding systems that can monitor and optimize welding processes.
Sustainability in welding: As the world becomes more environmentally conscious, sustainability is becoming increasingly important in welding. Efforts are being made to reduce the environmental impact of welding processes, such as developing more energy-efficient welding technologies, using eco-friendly filler materials, and recycling welding materials.
Welding Safety
Welding can be a hazardous process, and proper safety measures must be taken to prevent accidents and injury. Here are some of the key aspects of welding safety:
Hazards associated with welding: The hazards associated with welding include exposure to radiation, electric shock, fire and explosion, toxic fumes and gases, and noise. These hazards can cause severe injury or death if proper safety measures are not followed.
Personal protective equipment: Personal protective equipment (PPE) is critical in protecting welders from the hazards of welding. PPE includes welding helmets, goggles, gloves, aprons, respirators, and ear protection.
Fire prevention measures: Welding creates sparks and intense heat, which can start fires. Fire prevention measures, such as keeping the work area clean and free from flammable materials, having fire extinguishers nearby, and having a fire watch during and after welding, are essential in preventing fires.
Health effects of welding fumes and gases: Welding fumes and gases can cause health problems, such as metal fume fever, lung cancer, and neurological effects. Proper ventilation and respiratory protection are critical in preventing exposure to welding fumes and gases.
FAQs
What is welding in simple words?
Welding is a process of joining two or more pieces of metal together using heat, pressure, or a combination of both to create a permanent bond.
Why is welding used?
Welding is used to join two or more pieces of metal together to create a permanent bond. It is used in various industries, including automotive, construction, and manufacturing, to produce high-quality, durable products and structures.
What is welding called?
Welding is called a process of joining two or more pieces of metal together using heat, pressure, or a combination of both to create a permanent bond.
What are the 5 types of weld?
The five types of weld are butt weld, corner weld, lap weld, tee weld, and edge weld.
What is the principle of welding?
The principle of welding is to join two or more pieces of metal together using heat, pressure, or a combination of both to create a permanent bond.
Which gas is used in welding?
Different gases can be used in welding depending on the type of welding process being used. Some of the gases commonly used in welding are argon, carbon dioxide, helium, and hydrogen.
What are the 3 main types of welding?
The three main types of welding are MIG welding, TIG welding, and Stick welding.
Why CO2 is used in welding?
CO2 is commonly used in welding because it is inexpensive and readily available. It can be used as a shielding gas to protect the weld from the atmosphere and prevent oxidation.
What is welding flux?
Welding flux is a substance used in some welding processes to protect the weld from atmospheric contamination and provide a clean surface for welding. It can also act as a deoxidizer to remove impurities from the metal.
What is the formula of welding gas?
There is no single formula for welding gas as different types of welding processes use different gases or gas mixtures. For example, the formula for pure argon gas used in TIG welding is simply Ar, while the formula for a common MIG welding gas mixture of 75% Argon and 25% CO2 is Ar/CO2 75/25.
Conclusion
In conclusion, welding is a critical process that plays a vital role in various industries, including automotive, construction, and manufacturing. Here are some key takeaways from this discussion:
- Welding is the process of joining two or more metal parts together using heat, pressure, or a combination of both.
- There are several types of welding processes, such as arc welding, gas welding, and resistance welding, each with its unique advantages and challenges.
- Proper preparation, joint design, filler material selection, and welding techniques are essential for achieving high-quality welds.
- Welding materials can vary widely in their properties, making it challenging to weld different materials together. However, various techniques can be used to weld dissimilar materials.
- Welding can be hazardous, and proper safety measures must be taken to prevent accidents and injury.
- The future of welding is marked by advancements in technology, increased automation, the integration of Industry 4.0 technologies, and a focus on sustainability.