What is Whipping Welding?
Introduction
Definition of Whipping Welding
Whipping welding is a specialized welding technique that involves the use of a circular or zigzag motion to create weld beads. This technique is characterized by the rhythmic back-and-forth movement of the welding torch or electrode. The motion creates overlapping weld beads that provide strength and improve weld quality.
Importance of Whipping Welding
Whipping welding is an important welding technique that offers a range of advantages over other welding methods. The technique provides better control of heat input and weld penetration, allowing for improved quality and aesthetics of the finished weld. It is also a faster welding process than some other methods, due to the increased deposition rates.
Purpose of the article
The purpose of this article is to provide a comprehensive understanding of whipping welding, including its techniques, applications, and advantages. It will explain the basic principles of whipping welding, how it differs from other welding techniques, and the types of materials it can be used for. Additionally, the article will cover the advantages and disadvantages of whipping welding, along with the necessary equipment and safety precautions required to perform the technique safely. Finally, the article will explore the various applications of whipping welding in industrial settings, and the future prospects of this important welding technique. By the end of this article, readers will have a clear understanding of whipping welding and its potential benefits.
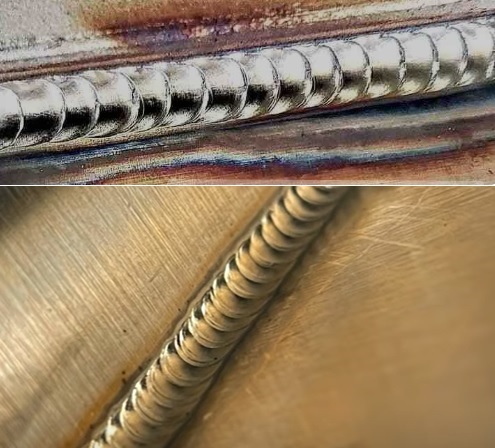
Understanding Whipping Welding
How Whipping Welding is different from other welding techniques
Whipping welding differs from traditional straight-line welding techniques such as stringer beads or weave beads. In whipping welding, the circular or zigzag motion of the welding torch or electrode creates a wider weld bead and distributes heat more evenly. This results in improved fusion between the base metal and the filler material, as well as a stronger and more aesthetically pleasing weld. Additionally, the motion of the welding torch or electrode in whipping welding enables better control of heat input and weld penetration, which is not possible with traditional welding techniques.
The basic principle of Whipping Welding
The basic principle of whipping welding involves oscillating the welding torch or electrode in a controlled pattern while maintaining a steady welding speed. The motion creates overlapping weld beads that provide strength and improve weld quality. The direction of the whip motion can be either circular or zigzag, depending on the application and the welding process being used. The whip pattern must be consistent to ensure a uniform weld bead and penetration.
Types of materials that can be used for Whipping Welding
Whipping welding can be applied to various materials such as steel, aluminum, stainless steel, and other alloys. The technique is particularly effective for welding thin sheets of metal, as it provides better control of heat input and reduces the risk of burn-through or distortion.
Advantages of Whipping Welding over other welding techniques
Whipping welding offers several advantages over other welding techniques. First, it provides better control of heat input, reducing the risk of distortion or burn-through. Second, the improved fusion between the base metal and the filler material results in a stronger and more aesthetically pleasing weld. Third, the increased deposition rates in whipping welding can lead to faster welding times, making it a more efficient welding process overall.
Disadvantages of Whipping Welding
While whipping welding offers many advantages, there are also some potential disadvantages to consider. The technique requires skilled operators to maintain a consistent whip pattern and travel speed, which can be challenging for novice welders. Additionally, whipping welding may produce more spatter compared to some other welding techniques, which can be an issue in certain applications. Finally, some welding processes may require specific equipment or techniques to perform whipping welding effectively, which can add to the overall cost of the welding process.
Techniques for Whipping Welding
Equipment needed for Whipping Welding
The equipment needed for whipping welding includes a welding machine, a welding torch or electrode holder, and a suitable filler material. The welding machine should be capable of providing sufficient amperage and voltage for the welding process being used. The welding torch or electrode holder should be compatible with the welding machine and suitable for the material being welded. A suitable filler material should be selected based on the type of material being welded and the welding process being used.
Safety precautions when performing Whipping Welding
Whipping welding poses potential safety hazards, and it is essential to take appropriate safety precautions when performing the technique. Safety gear such as welding helmets, gloves, and protective clothing should be worn to protect against the hazards of welding, including ultraviolet radiation, hot sparks, and fumes. The work area should be properly ventilated to reduce the risk of exposure to welding fumes. Operators should also ensure that the welding machine and equipment are properly grounded to prevent electrical shock hazards.
Step-by-step process of Whipping Welding
The step-by-step process for whipping welding includes the following:
- Prepare the workpiece by cleaning the surface to be welded and ensuring that it is free from rust, dirt, and other contaminants.
- Choose the appropriate filler material and prepare it for use.
- Set the welding machine to the appropriate amperage and voltage for the welding process being used.
- Hold the welding torch or electrode holder at the desired angle and initiate the arc.
- Begin the whipping motion in a consistent circular or zigzag pattern while maintaining a steady travel speed.
- Apply the filler material as needed to create the desired weld bead size and shape.
- Continue the whipping motion until the desired length of the weld is completed.
- Allow the weld to cool before removing any clamps or fixtures.
Common problems encountered in Whipping Welding and how to solve them
Some common problems encountered in whipping welding include insufficient penetration, porosity, and spatter. Insufficient penetration occurs when the weld bead does not penetrate deeply enough into the base metal, resulting in a weak weld. This can be solved by adjusting the travel speed or increasing the amperage. Porosity occurs when gas pockets form within the weld bead, weakening the joint. This can be solved by ensuring that the welding area is properly cleaned and ventilated, and that the correct filler material is used. Spatter occurs when molten metal splatters onto the surrounding area, creating a mess and potential safety hazard. This can be reduced by adjusting the welding parameters or using anti-spatter compounds.
Applications of Whipping Welding
Industrial applications of Whipping Welding
Whipping welding is widely used in a variety of industrial applications. Its ability to produce strong and visually appealing welds has made it popular in the fabrication of metal structures, piping systems, and automotive components. Additionally, it is used in the construction of ships and other marine structures, as well as in the manufacturing of electrical and electronic components.
Comparison of Whipping Welding with other welding techniques
Whipping welding offers several advantages over other welding techniques. It is a versatile process that can be used with a wide range of materials, including stainless steel, aluminum, and titanium. It produces high-quality welds with minimal distortion, resulting in strong and durable joints. Additionally, whipping welding is a fast process that can be completed quickly, reducing production time and costs.
However, whipping welding does have some limitations. It is not suitable for welding thick materials or for producing welds in areas with limited access. Additionally, it can be challenging to master the technique, and it requires a high level of skill and experience to produce consistent and high-quality welds.
Future prospects of Whipping Welding
Whipping welding is expected to continue to play an important role in industrial welding applications in the future. Advances in welding technology, such as the development of automated welding systems and the integration of robotics, are likely to further improve the efficiency and quality of whipping welding processes. Additionally, research is ongoing to explore the use of new materials and welding processes that may further expand the applications of whipping welding in industries such as aerospace and defense. Overall, whipping welding is a valuable welding technique that is likely to remain an important tool in the industrial welding arsenal for years to come.
FAQs
What is whipping in welding?
Whipping is a welding technique that involves oscillating the welding torch in a controlled motion to create a back-and-forth pattern. This technique is commonly used in MIG welding and TIG welding to produce a strong and visually appealing weld.
What is whipping technique?
The whipping technique is a welding technique where the welding torch is moved back and forth in a controlled motion, creating a pattern in the weld bead. This technique is used to improve penetration and produce a stronger weld.
What is whipping MIG welding?
Whipping MIG welding is a welding technique that involves moving the welding torch back and forth in a controlled motion while feeding the welding wire into the joint. This technique is used to improve penetration and produce a stronger weld.
What is the stitch or whip technique welding?
The stitch or whip technique welding is a welding technique where the welding torch is moved back and forth in a controlled motion to create a stitch or whip pattern in the weld bead. This technique is used to improve penetration and produce a stronger weld.
What is the function of whipping?
The function of whipping in welding is to improve penetration and produce a stronger weld. The back-and-forth motion of the welding torch helps to melt and fuse the base metals, creating a stronger joint.
What is whipping line used for?
The whipping line is used in welding to guide the welding torch in a back-and-forth motion, creating a whipping pattern in the weld bead. This helps to improve penetration and produce a stronger weld.
What are the 3 types of MIG welding?
The three types of MIG welding are short circuit transfer, spray transfer, and pulsed spray transfer.
What are the two types of MIG?
The two types of MIG welding are MIG (Metal Inert Gas) welding and MAG (Metal Active Gas) welding. MIG welding uses an inert gas such as argon or helium, while MAG welding uses an active gas such as carbon dioxide.
Why is it called MIG welding?
MIG welding is called “Metal Inert Gas” welding because it uses an inert gas, such as argon or helium, to shield the weld from atmospheric contamination.
Conclusion
In this article, we have explored the technique of whipping welding, which involves moving the welding torch in a back-and-forth motion to produce a strong and visually appealing weld. We have discussed the basic principles of whipping welding, the equipment needed for the technique, the safety precautions that need to be taken, and the step-by-step process for performing the technique. We have also examined the advantages and disadvantages of whipping welding, the different types of materials that can be used, and the applications of the technique. Whipping welding is a valuable technique that can produce strong, high-quality welds. However, it requires a certain level of skill and practice to master. It is important to take the necessary safety precautions and use the appropriate equipment when performing whipping welding to ensure a safe and successful welding operation.