Electrogas Welding: Revolutionizing Industrial Welding
Introduction
Electrogas welding, also known as EGW, is a fusion welding process primarily used for thick materials, typically ranging from 1 inch to several inches in thickness. It involves the application of heat generated by electrical resistance to melt and join metals together, forming a strong, durable bond.
Definition History of Electrogas Welding
Electrogas welding is a fusion welding process that utilizes electrical arc heat and a continuously fed consumable electrode wire to join thick metal sections in a single pass. The process involves the creation of an arc between the base material and the electrode wire, which melts the materials, forming a weld pool. Simultaneously, a flux blanket shields the molten weld pool from atmospheric contamination, ensuring a clean and robust weld.
The roots of electrogas welding can be traced back to the mid-20th century when it emerged as an evolution of the traditional gas metal arc welding (GMAW) process. Its development was primarily driven by the need to enhance productivity and weld quality in industries dealing with large-scale fabrication of heavy structures. Over the years, advancements in welding technology and materials have refined the electrogas welding process, making it a preferred choice for numerous applications requiring high deposition rates and superior weld integrity.
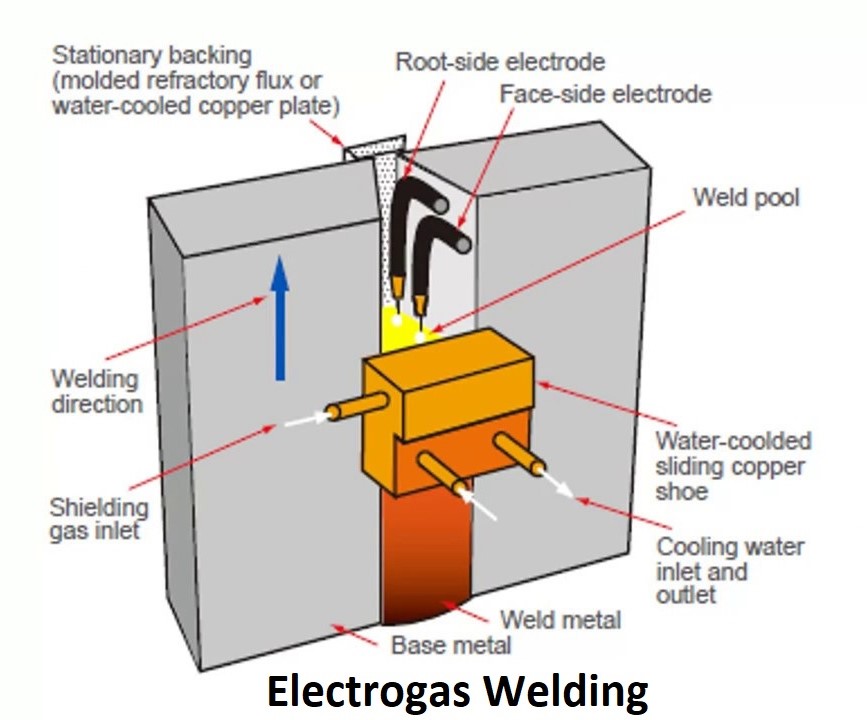
Understanding Electrogas Welding Process
Electrogas welding (EGW) is a specialized welding process that offers high productivity and efficiency, particularly suitable for joining thick metal sections in a single pass. This section provides an in-depth explanation of the electrogas welding process, detailing its key aspects, components, and equipment requirements, along with a comparison with other popular welding techniques.
Explanation of the Electrogas Welding Process
The electrogas welding process involves the following key steps:
- Preparation: Before welding, the workpieces to be joined are cleaned and properly aligned to ensure precise assembly.
- Setup: A welding power source supplies the necessary electrical energy to create an arc between the base metal and a continuously fed consumable electrode wire. The welding machine also controls parameters such as voltage, current, and wire feed speed.
- Arc Initiation: An arc is initiated between the electrode wire and the workpiece, generating intense heat that melts the base metal and the electrode wire, forming a molten weld pool.
- Shielding: A flux blanket is continuously fed to cover the weld pool, protecting it from atmospheric contamination and preventing oxidation. The flux also helps shape the weld bead and facilitates slag removal.
- Welding Progression: The welding process progresses along the joint, with the molten weld pool solidifying behind the welding torch. As the torch moves, it maintains the necessary arc length and welding parameters to ensure proper fusion and penetration.
- Cooling and Solidification: Once the welding is complete, the weld cools and solidifies, forming a strong and durable joint between the workpieces.
Components and Equipment Required for Electrogas Welding
The primary components and equipment required for electrogas welding include:
- Welding Power Source: Provides the electrical energy necessary to generate the welding arc. It must be capable of delivering high currents to accommodate the thick metal sections typically welded using the electrogas process.
- Electrode Wire Feeder: Feeds the consumable electrode wire continuously into the welding arc at a controlled rate. The wire feeder ensures a steady supply of filler material, maintaining consistent weld bead geometry and deposition rates.
- Welding Torch: Houses the electrode wire and guides the welding arc along the joint. It also incorporates mechanisms for controlling the flow of shielding gas and flux to protect the weld pool.
- Flux Delivery System: Supplies the flux blanket to cover the weld pool, preventing atmospheric contamination and facilitating slag removal. The flux may be in the form of granules or powder, depending on the welding application.
- Gas Supply System: Provides the shielding gas, typically a mixture of argon and carbon dioxide, to protect the weld pool from oxidation and improve weld quality.
- Welding Positioning Equipment: In some cases, welding manipulators or positioners are used to precisely position the workpieces and welding torch, especially for vertical or overhead welding applications.
Comparison with Other Welding Techniques (e.g., MIG, TIG)
Electrogas welding differs from other popular welding techniques such as MIG (Metal Inert Gas) and TIG (Tungsten Inert Gas) in several key aspects:
- Deposition Rates: Electrogas welding offers higher deposition rates compared to MIG and TIG welding, making it particularly suitable for welding thick metal sections quickly.
- Suitability for Thick Materials: Electrogas welding excels in welding thick materials, whereas MIG and TIG welding are more commonly used for thinner materials and precision welding applications.
- Weld Quality: While all three techniques can produce high-quality welds, electrogas welding may be preferred for applications where productivity and efficiency are paramount, while MIG and TIG welding offer greater versatility and control over weld bead geometry.
- Welding Positions: Electrogas welding is typically limited to flat and horizontal welding positions due to the nature of the process, whereas MIG and TIG welding can be performed in various positions, including vertical and overhead.
Operating Principles of Electrogas Welding
Electrogas welding (EGW) relies on several fundamental principles to achieve efficient and high-quality welds. This section delves into the key operating principles of electrogas welding, covering aspects such as the power source, gas supply, electrode and wire feeding mechanisms, as well as heat generation and control.
Power Source and Electrical Circuitry
The power source in electrogas welding plays a crucial role in providing the necessary electrical energy to sustain the welding arc. Typically, electrogas welding utilizes a constant voltage (CV) power source, which ensures a stable arc and consistent weld bead geometry. The electrical circuitry includes:
- Transformer or Rectifier: Converts the incoming AC or DC electrical power to the desired welding voltage and current levels suitable for the electrogas welding process.
- Welding Control Unit: Regulates the welding parameters such as voltage, current, and wire feed speed, allowing for precise control over the welding process.
- Electrode Circuit: Completes the electrical circuit by connecting the electrode wire to the positive terminal of the power source. The electrical current flows from the power source through the electrode wire, creating an arc between the electrode and the workpiece.
Gas Supply and Shielding Gas Selection
Shielding gas plays a critical role in electrogas welding by protecting the weld pool from atmospheric contamination and ensuring high-quality welds. The gas supply system consists of:
- Gas Cylinder: Stores the shielding gas, typically a mixture of argon and carbon dioxide or other inert gases, depending on the welding application.
- Regulator and Flowmeter: Regulates the flow rate of the shielding gas to maintain the desired gas coverage over the weld pool. The flowmeter allows precise adjustment of the gas flow rate, ensuring optimal shielding and weld quality.
- Gas Delivery System: Transports the shielding gas from the cylinder to the welding torch, where it is dispensed to create a protective atmosphere around the weld pool.
The selection of shielding gas depends on factors such as the base metal composition, welding parameters, and desired weld characteristics, with different gas mixtures offering varying levels of penetration, arc stability, and spatter control.
Electrode and Wire Feeding Mechanisms
In electrogas welding, a continuously fed consumable electrode wire serves as the filler material, providing the necessary material for the weld joint. The electrode and wire feeding mechanisms consist of:
- Electrode Holder or Gun: Houses the electrode wire and guides it to the welding arc. The electrode holder incorporates mechanisms for controlling the wire feed speed and maintaining proper arc length during welding.
- Wire Feeder: Supplies the electrode wire from a spool to the welding torch at a controlled rate. The wire feeder ensures a steady and consistent feed of filler material, contributing to uniform weld bead formation and deposition rates.
Heat Generation and Control
Heat generation in electrogas welding is primarily achieved through the electrical arc between the electrode wire and the workpiece. The arc produces intense heat, melting both the base metal and the electrode wire to form a molten weld pool. Heat control is essential to achieve proper fusion, penetration, and weld quality, which is accomplished through:
- Welding Parameters: Parameters such as voltage, current, and wire feed speed are adjusted to control the heat input and welding process variables. Maintaining optimal parameters ensures proper fusion and penetration without causing excessive distortion or defects in the weld joint.
- Travel Speed: The speed at which the welding torch moves along the joint affects heat input and weld bead geometry. Adjusting the travel speed allows for fine-tuning of the heat input and ensures consistent weld quality throughout the welding process.
Advantages and Limitations of Electrogas Welding
Electrogas welding (EGW) offers several advantages that make it a preferred choice for many welding applications. However, like any welding process, it also has its limitations. This section explores the advantages and limitations of electrogas welding in detail.
Advantages:
- High Deposition Rates: Electrogas welding is known for its exceptionally high deposition rates, allowing for rapid welding of thick metal sections in a single pass. This high-speed deposition results in increased productivity and reduced welding time compared to other welding processes.
- Suitable for Thick Materials: Electrogas welding excels in welding thick materials, making it particularly well-suited for heavy fabrication applications where deep penetration and high weld integrity are essential. The process can effectively join metal plates ranging from several millimeters to several inches in thickness.
- Reduced Distortion: The concentrated heat input and high deposition rates of electrogas welding contribute to reduced distortion in the welded components. This is particularly advantageous in applications where dimensional accuracy and minimal distortion are critical, such as in shipbuilding and structural steel fabrication.
- Improved Productivity: Electrogas welding offers improved productivity compared to conventional welding processes, thanks to its high deposition rates and single-pass welding capability. This translates to faster project completion times, reduced labor costs, and increased overall efficiency in manufacturing operations.
Limitations:
- Limited to Flat and Horizontal Welding Positions: One of the primary limitations of electrogas welding is its restriction to flat and horizontal welding positions. Vertical and overhead welding positions are challenging to achieve with this process, limiting its applicability in certain welding scenarios.
- Requires Skilled Operators: Electrogas welding demands skilled and experienced operators to ensure proper setup, adjustment of welding parameters, and control of the welding process. Achieving high-quality welds with electrogas welding requires expertise in arc control, flux handling, and joint preparation techniques.
- Initial Setup Costs: Electrogas welding typically involves higher initial setup costs compared to some other welding processes. The equipment and infrastructure required for electrogas welding, including specialized power sources, wire feeders, and flux delivery systems, can represent a significant investment for welding operations.
Applications of Electrogas Welding
Electrogas welding (EGW) finds extensive use across various industries due to its capability to efficiently join thick metal sections while maintaining high weld quality. This section explores some of the key applications of electrogas welding in different industrial sectors.
Shipbuilding and Offshore Structures:
Electrogas welding is widely employed in the shipbuilding industry for constructing large-scale vessels, offshore platforms, and marine structures. The process’s ability to weld thick steel plates in a single pass makes it invaluable for fabricating hulls, decks, and structural components of ships and offshore installations. The high deposition rates of electrogas welding contribute to faster production times, ensuring timely completion of maritime projects while meeting stringent quality standards and regulatory requirements.
Bridge Construction:
In the construction of bridges and infrastructure projects, electrogas welding plays a vital role in joining heavy steel girders, beams, and structural components. The process’s capability to weld thick materials efficiently and with minimal distortion makes it well-suited for fabricating bridge components, including trusses, supports, and deck sections. Electrogas welding ensures structural integrity and durability, essential for bridges spanning rivers, highways, and railways, where safety and reliability are paramount.
Pressure Vessel Fabrication:
Industries such as petrochemical, power generation, and aerospace rely on electrogas welding for manufacturing pressure vessels, boilers, and storage tanks. The process’s high deposition rates and ability to weld thick materials ensure the integrity and strength of these critical components, capable of withstanding high temperatures, pressures, and corrosive environments. Electrogas welding is instrumental in producing pressure vessels for storing and transporting gases, liquids, and chemicals safely and efficiently.
Pipeline Welding:
Electrogas welding plays a significant role in the construction and maintenance of pipelines for transporting oil, gas, and other fluids over long distances. The process’s high productivity and capability to weld thick pipeline sections in a single pass contribute to the rapid deployment of energy infrastructure projects. Whether in onshore or offshore applications, electrogas welding ensures reliable and leak-free pipelines, meeting the stringent quality and safety standards of the oil and gas industry.
Heavy Equipment Manufacturing:
In the fabrication of heavy machinery and equipment, electrogas welding is widely used to join structural components and assemblies. Industries such as mining, agriculture, construction, and transportation rely on the process to produce robust and durable equipment capable of withstanding harsh operating conditions. Electrogas welding ensures the integrity and strength of weld joints in heavy equipment, contributing to the reliability and longevity of these essential industrial assets.
Quality Control and Inspection in Electrogas Welding
Quality control and inspection are critical aspects of the electrogas welding process to ensure the integrity and reliability of welded components. This section explores the various methods and criteria used for quality control and inspection in electrogas welding.
Non-destructive Testing Methods:
Non-destructive testing (NDT) methods are essential for evaluating the quality of welds without causing damage to the welded components. Some common NDT methods used in electrogas welding include:
- Radiographic Testing (RT): RT involves exposing the welded joint to X-rays or gamma rays to create a radiographic image. This method is effective for detecting internal defects such as porosity, lack of fusion, and incomplete penetration.
- Ultrasonic Testing (UT): UT utilizes high-frequency sound waves to detect flaws within the welded material. Ultrasonic probes are used to send and receive sound waves, and the reflected waves are analyzed to identify defects such as cracks, inclusions, and bond integrity.
- Magnetic Particle Testing (MT): MT is used to detect surface and near-surface defects in ferromagnetic materials. A magnetic field is applied to the welded component, and iron particles are applied to the surface. Any discontinuities, such as cracks or lack of fusion, will create magnetic flux leakage, indicating the presence of defects.
- Liquid Penetrant Testing (PT): PT involves applying a liquid penetrant to the surface of the welded joint, which seeps into surface-breaking defects. After excess penetrant is removed, a developer is applied to draw out the penetrant from the defects, making them visible for inspection.
These NDT methods are employed to identify defects and discontinuities in welds, ensuring compliance with welding standards and specifications.
Visual Inspection Criteria:
Visual inspection is a fundamental quality control method that involves examining welds visually to assess their appearance and detect surface imperfections. Some common criteria evaluated during visual inspection of electrogas welds include:
- Weld Profile: The shape and geometry of the weld bead are inspected to ensure proper fusion and penetration into the base metal.
- Surface Smoothness: The surface of the weld should be smooth and free from irregularities such as undercut, overlap, and spatter.
- Discontinuities: Visual inspection is used to identify defects such as cracks, porosity, lack of fusion, and incomplete penetration.
- Weld Reinforcement: The amount of weld reinforcement, or excess weld metal on the surface, is evaluated to ensure it meets specified requirements.
Visual inspection criteria provide immediate feedback on weld quality and can help identify defects that may require further examination using NDT methods.
Mechanical Testing Requirements:
In addition to NDT and visual inspection, mechanical testing is often performed to assess the mechanical properties and performance of welds. Some common mechanical testing requirements for electrogas welding include:
- Tensile Testing: Tensile testing involves subjecting welded specimens to tensile forces to evaluate their strength and ductility. This test helps determine the ultimate tensile strength, yield strength, and elongation of the weld metal and heat-affected zone.
- Bend Testing: Bend testing is used to assess the ductility and soundness of welded joints by bending specimens to a specified angle without fracture. This test can detect defects such as cracks and lack of fusion along the bend line.
- Charpy Impact Testing: Charpy impact testing measures the impact energy absorbed by a welded specimen subjected to a sudden impact load. This test assesses the toughness and notch sensitivity of the weld metal and heat-affected zone, particularly in applications where the welded component may experience dynamic loading or impact.
Safety Considerations in Electrogas Welding
Electrogas welding (EGW) presents various hazards to operators and bystanders alike. Ensuring safety during the welding process is paramount to prevent accidents and injuries. This section discusses key safety considerations and precautions in electrogas welding.
Electrical Hazards and Precautions:
Electric Shock: Electrogas welding involves high electrical currents, posing a risk of electric shock to operators. To mitigate this hazard:
- Ensure all electrical equipment is properly grounded.
- Use insulated gloves and tools when working on live electrical components.
- Avoid contact with the electrode, workpiece, and conductive surfaces while welding.
Arc Flash: The welding arc produces intense ultraviolet (UV) radiation, which can cause arc flash burns to the skin and eyes. To minimize the risk of arc flash injuries:
- Wear appropriate welding helmets with UV-filtering lenses.
- Use welding curtains or screens to shield bystanders from the welding arc.
- Ensure adequate ventilation to dissipate heat and fumes generated during welding.
Electrical Fires: Electrical fires can occur due to short circuits, overheating, or improper wiring. To prevent electrical fires:
- Inspect electrical cables and connections for damage or wear regularly.
- Use circuit breakers or fuses to protect against overcurrents.
- Have fire extinguishing equipment, such as fire blankets or extinguishers, readily available.
Gas Handling and Ventilation:
Gas Leaks: Leakage of shielding gases such as argon and carbon dioxide can pose a suffocation hazard in confined spaces. To prevent gas leaks:
- Inspect gas cylinders, hoses, and connections for leaks before use.
- Store gas cylinders in well-ventilated areas away from heat sources and ignition hazards.
- Use gas detectors to monitor gas concentrations in confined spaces.
Ventilation: Proper ventilation is essential to remove welding fumes, gases, and airborne contaminants from the work area. To ensure adequate ventilation:
- Position welding equipment near exhaust hoods or ventilation fans.
- Use local exhaust ventilation systems to capture fumes at the source.
- Avoid welding in enclosed spaces without proper ventilation.
Gas Cylinder Handling: Handling and transporting gas cylinders require caution to prevent accidents and injuries. Follow these precautions:
- Secure gas cylinders in an upright position with appropriate restraints.
- Use a cylinder cart or trolley to transport cylinders safely.
- Avoid dropping or mishandling cylinders to prevent damage and leaks.
Personal Protective Equipment (PPE) Requirements:
- Welding Helmet: Protects the eyes and face from UV radiation, sparks, and debris generated during welding.
- Welding Gloves: Insulated gloves provide protection against electric shock, heat, and molten metal splatter.
- Welding Clothing: Wear flame-resistant clothing to protect against burns and sparks. Long sleeves and pants help prevent skin exposure.
- Respiratory Protection: Use a respirator or welding fume mask to protect against inhalation of welding fumes and airborne contaminants.
- Safety Glasses: Wear safety glasses with side shields to protect against flying debris and UV radiation.
- Ear Protection: Use earplugs or earmuffs to protect against noise generated by welding equipment and machinery.
FAQs
Is electrogas welding suitable for thin materials?
No, electrogas welding is primarily used for thick materials due to its high deposition rates and deep penetration capabilities.
What types of metals can be welded using electrogas welding?
Electrogas welding is commonly used for welding steel and its alloys, particularly in industries such as shipbuilding and construction.
Are there any environmental concerns associated with electrogas welding?
Electrogas welding can produce fumes and gases that may pose health and environmental risks if not properly controlled. Adequate ventilation and safety measures are essential.
How does electrogas welding compare to other welding methods in terms of speed?
Electrogas welding typically offers higher deposition rates compared to many other welding methods, making it faster for welding thick materials.
What are some key safety considerations for operators using electrogas welding equipment?
Operators should wear appropriate protective gear, ensure proper ventilation, and implement fire prevention measures to minimize risks associated with electrogas welding.
Conclusion
Electrogas welding stands as a testament to human ingenuity, offering unparalleled efficiency and precision in joining thick materials. With its wide-ranging applications and ongoing technological advancements, it continues to revolutionize industrial welding, shaping the future of manufacturing and construction.