Twin Carbon Arc Welding: Unleashing Precision and Power
Introduction
Welcome to the realm of Twin Carbon Arc Welding, a revolutionary welding technique that has taken the metalworking industry by storm. In this article, we will delve into the intricate details of Twin Carbon Arc Welding, exploring its features, applications, advantages, and much more. If you’re curious about this innovative welding method and how it can revolutionize your projects, you’ve come to the right place.
Twin Carbon Arc Welding
Twin Carbon Arc Welding, often referred to as TCAW, is a cutting-edge welding process that employs the heat generated between two carbon electrodes to melt and fuse metal pieces together. This technique is renowned for its exceptional precision and remarkable power, making it a preferred choice for various applications across industries.
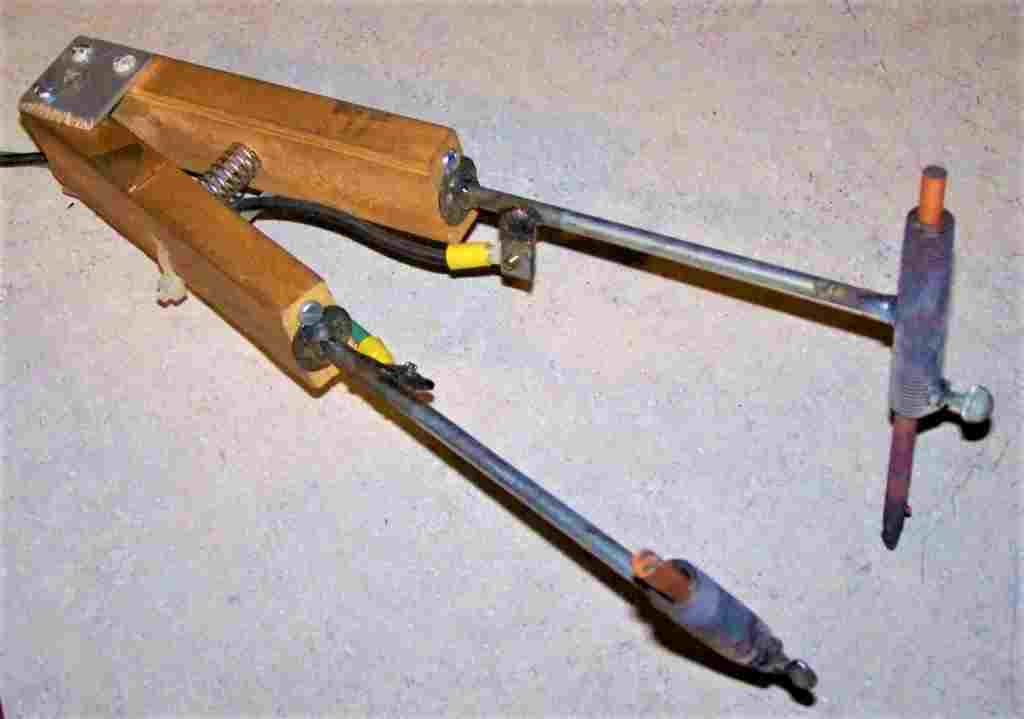
The Dynamics of Twin Carbon Arc Welding
TCAW operates on the principle of creating an electric arc between two carbon electrodes, which act as both the heat source and the filler material. The intense heat generated by the electric arc melts the metal surfaces, creating a pool of molten metal that solidifies upon cooling, forming a strong and durable weld joint.
Applications of Twin Carbon Arc Welding
TCAW finds its utility across a wide spectrum of industrial sectors, from aerospace to automotive, construction to manufacturing. Some prominent applications include:
- Aerospace Fabrication: TCAW is utilized in crafting precision components for aircraft and spacecraft, ensuring structural integrity and performance.
- Automotive Manufacturing: The technique is employed in assembling various automotive parts, from chassis components to exhaust systems, enhancing the overall durability.
- Shipbuilding: TCAW is used to create robust welds in shipbuilding, contributing to the seaworthiness and longevity of vessels.
- Oil and Gas Pipelines: TCAW ensures secure joints in pipelines, safeguarding against leaks and ensuring efficient transportation of resources.
- Structural Steelwork: It plays a vital role in constructing steel frameworks for buildings and bridges, guaranteeing stability and safety.
- Heavy Machinery Fabrication: TCAW is crucial in manufacturing heavy machinery, such as excavators and cranes, ensuring reliability under extreme conditions.
Advantages of Twin Carbon Arc Welding
Embracing Twin Carbon Arc Welding offers an array of benefits that contribute to its rising popularity:
- Precision: TCAW’s focused heat source allows for precise control over the welding process, leading to accurate and clean welds.
- High Strength: The concentrated heat results in strong welds with excellent mechanical properties, ensuring the longevity of welded components.
- Versatility: TCAW can be applied to various metals and alloys, expanding its range of applications.
- Speed and Efficiency: The efficient melting and solidification process leads to faster welding, saving valuable time in production.
- Reduced Distortion: The controlled heat input minimizes distortion in the welded pieces, maintaining their original shape.
Twin Carbon Arc Welding in Action
Let’s take a closer look at the step-by-step process of executing Twin Carbon Arc Welding:
- Preparation: Thoroughly clean and prepare the surfaces to be welded, ensuring the removal of any contaminants or impurities.
- Electrode Placement: Position the two carbon electrodes at the desired welding location, maintaining an appropriate distance.
- Arc Initiation: Create an electric arc between the electrodes, generating intense heat that melts the metal surfaces.
- Weld Pool Formation: As the metal surfaces liquefy, a weld pool is formed, ready for the fusion process.
- Fusion: Control the movement of the electrodes to guide the weld pool’s solidification and fusion, creating a seamless joint.
- Cooling and Solidification: Allow the molten metal to cool and solidify, forming a robust weld joint with exceptional strength.
Disadvantages of Twin Carbon Arc Welding
- Complexity: TCAW requires skilled operators due to its complex setup and precise control demands, potentially increasing labor costs.
- Equipment Costs: The specialized equipment needed for TCAW can be expensive to acquire and maintain, impacting overall project budgets.
- Limited Portability: The setup for TCAW may not be as portable as other welding methods, making it less suitable for remote or on-site welding.
Limitations in Comparison to Other Carbon Welding Techniques
- Shielded Metal Arc Welding (SMAW): While TCAW offers higher precision, SMAW is more versatile and can be used in a broader range of environments.
- Gas Metal Arc Welding (GMAW): TCAW’s intricate setup may be less suitable for high-volume production compared to the efficiency of GMAW.
- Submerged Arc Welding (SAW): TCAW’s precision is valuable, but SAW’s deep penetration capability makes it preferable for thicker materials.
FAQs
Is Twin Carbon Arc Welding suitable for delicate materials?
Absolutely! TCAW’s precise control makes it an ideal choice for delicate materials, ensuring minimal heat-affected zones.
What safety measures are crucial during TCAW?
Safety goggles, gloves, and fire-resistant clothing are essential to protect against arc flashes and sparks.
Can TCAW be automated?
Yes, TCAW can be automated using specialized equipment, enhancing efficiency and consistency.
Does TCAW produce harmful fumes?
Like other welding processes, TCAW can emit fumes, making proper ventilation vital to ensure a safe working environment.
What metals can be welded using TCAW?
TCAW is versatile and can weld various metals, including steel, stainless steel, aluminum, and more.
How does TCAW compare to other welding techniques?
TCAW’s combination of precision and power sets it apart, providing high-strength welds with minimal distortion.
Conclusion
In conclusion, Twin Carbon Arc Welding stands as a testament to human ingenuity, combining precision and power to create exceptional welds across diverse applications. Its remarkable attributes make it an invaluable tool in the arsenal of welders and manufacturers, shaping industries and driving innovation. As you embark on your welding journey, consider harnessing the potential of Twin Carbon Arc Welding to elevate your projects to new heights.