Weld Testing Methods
Introduction
Weld testing is a crucial step in the manufacturing process of many industrial products, ensuring the strength and reliability of the welded joints. The objective of weld testing is to detect any defects or inconsistencies that might affect the structural integrity of the final product. Weld testing involves a variety of methods and techniques, each designed to assess different aspects of the welded joint. The most common methods include visual inspection, dye penetrant inspection (DPI), magnetic particle inspection (MPI), ultrasonic testing (UT), and radiographic testing (RT). These methods are performed at various stages of the welding process, from initial quality control to final inspection.
Welding is a critical operation that determines the strength and reliability of many industrial products. The integrity of the welded joint must be ensured to prevent failure and ensure the safety of the end-users. Weld testing is critical to ensuring the quality and reliability of the final product and helps to prevent costly defects and repairs. By identifying and correcting any inconsistencies early in the process, weld testing can save time, money, and resources, ultimately improving the efficiency of the manufacturing process.
What is welding testing?
Welding testing refers to the process of evaluating the quality and strength of a weld to ensure that it meets the required standards and specifications. Welding testing is an important step in the welding process, as it helps to ensure the integrity and reliability of the welded structure.
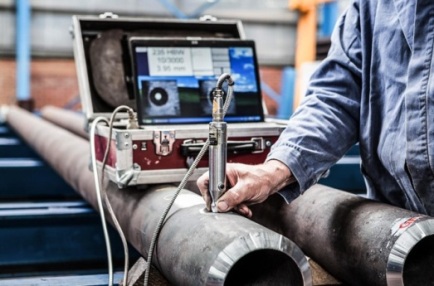
Types of Welding Testing
There are two different types of welding testing
2-Non-destructive Testing (NDT)
Destructive Testing
A destructive test is a type of test that involves deliberately damaging or destroying a test specimen in order to evaluate its properties or performance. In the field of welding, destructive testing is often used to verify the strength and quality of welds.
Destructive testing is typically performed by qualified professionals who are trained in the use of specialized equipment and procedures. It is important to carefully follow all safety guidelines and procedures when conducting destructive testing, as the process can be hazardous. There are several types of destructive tests that can be used to evaluate welds, including:
This test measures the maximum tensile load a weld can withstand before breaking.
Bend testing
This test involves bending a welded specimen to evaluate its resistance to cracking or breaking.
Notch testing
This test involves creating a notch or groove in a welded specimen and applying a tensile load to evaluate the weld’s resistance to fatigue.
Impact testing
This test involves striking a welded specimen with a heavy object to evaluate its resistance to impact.
Hardness testing
This test involves measuring the hardness of a welded specimen to determine its resistance to deformation.
Non-destructive Testing
Welding testing is an important step in ensuring the quality and reliability of welded structures, and it is often required by industry standards and regulations. By performing regular welding testing, welders can help to ensure the safety and integrity of the structures they work on. There are several different methods of welding non-destructive testing, including:
Visual Inspection
Visual inspection is a simple but effective method of welding testing that involves examining the weld visually to look for defects or imperfections. This can be done with the naked eye or with the aid of magnification, such as a magnifying glass or microscope. Visual inspection is often the first step in welding testing, and it can help to identify obvious defects such as porosity, undercut, or overlap.
Dye Penetrant Inspection (DPI)
Dye penetrant inspection involves applying a fluorescent dye to the surface of the weld and then using a black light to highlight any defects or cracks that may be present. This method is useful for detecting surface defects such as cracks and porosity.
Magnetic particle inspection
Magnetic particle inspection is a method of welding testing that involves applying a magnetic field to the weld and then using iron oxide or iron oxide-coated particles to detect any defects or cracks that may be present. This method is useful for detecting surface and subsurface defects in ferromagnetic materials.
Ultrasonic inspection
Ultrasonic inspection involves using high-frequency sound waves to inspect the weld for defects. This method is useful for detecting subsurface defects and is often used in conjunction with other welding testing methods.
Radiographic inspection
Radiographic inspection involves using X-rays or gamma rays to inspect the weld for defects. This method is useful for detecting internal defects such as porosity and lack of penetration, and it is often used for welds that are difficult to access visually.
FAQs
Which non-destructive test is most commonly used in welding?
The most commonly used non-destructive test in welding is Radiographic Testing (RT).
When should we consider using destructive testing?
Destructive testing is considered when it is necessary to obtain detailed information about the internal structure of a material or component that cannot be obtained through non-destructive methods.
What is the main purpose of destructive and non-destructive testing?
The main purpose of both destructive and non-destructive testing is to evaluate the quality and integrity of a material or component for the purpose of ensuring its reliability, performance, and safety. Non-destructive testing provides information without altering the component, while destructive testing provides more detailed information but alters the component in the process.
What are the limitations of destructive testing?
Limitations of destructive testing include that it is time-consuming, expensive, and alters the component being tested. Also, it can only provide information about the portion of the component that has been tested and can only be used once.
What is the most common purpose of non-destructive testing?
The most common purpose of non-destructive testing is to identify defects or discontinuities in a material or component that might affect its performance or safety.
What is the scope of non-destructive testing?
The scope of non-destructive testing is very broad, covering a variety of industries such as aerospace, nuclear power, oil and gas, and manufacturing, among others.
Which NDT makes defects easier?
Ultrasonic Testing (UT) is a non-destructive testing method that makes defects easier to identify.
Is sampling applicable to destructive testing?
Sampling is applicable to destructive testing, as it provides a small portion of the component to be tested to obtain information about the entire component.
What is the future of non-destructive testing?
The future of non-destructive testing is likely to see continued technological advancements, increasing automation and integration with artificial intelligence, and wider application in various industries.
Conclusion
In conclusion, weld testing is a crucial aspect of ensuring the quality and safety of welding processes in various industries. From traditional techniques such as visual inspection and x-rays to advanced techniques like ultrasonic and eddy current testing, the field of weld testing has come a long way. With the advancements in technology, the future trends in weld testing include the use of AI and robotics, non-destructive testing techniques, and the integration of virtual and augmented reality for training and inspection purposes. These developments are aimed at making weld testing more efficient, cost-effective, and accurate. Overall, the future of weld testing looks bright and holds tremendous potential for improving the welding industry.