Welding in the Oil and Gas Industry
Introduction
Welding plays a crucial role in the oil and gas industry due to its importance in the production and transportation of energy resources. The sector heavily relies on welding to ensure the integrity and reliability of various structures and equipment. Without welding, it would be challenging to construct and maintain the pipelines, storage tanks, refineries, and other critical infrastructure required for oil and gas operations.
The primary importance of welding in the oil and gas sector lies in its ability to join metal components together, creating strong and durable connections. This is essential for ensuring the structural integrity of pipelines and preventing leaks or failures that could lead to environmental damage, safety hazards, and economic losses.
In addition to pipeline construction, welding is utilized in various applications within the industry. It is extensively used in the fabrication and repair of pressure vessels, heat exchangers, valves, and other equipment used in the extraction, processing, and distribution of oil and gas. Welding also plays a crucial role in the construction of offshore platforms, subsea structures, and refineries. The transportation of oil and gas involves the use of pipelines, which often span long distances and traverse various terrains, including harsh environments such as deserts, arctic regions, and offshore installations. Welding ensures the integrity of these pipelines, enabling the safe and efficient transportation of resources from production sites to distribution networks and ultimately to consumers.
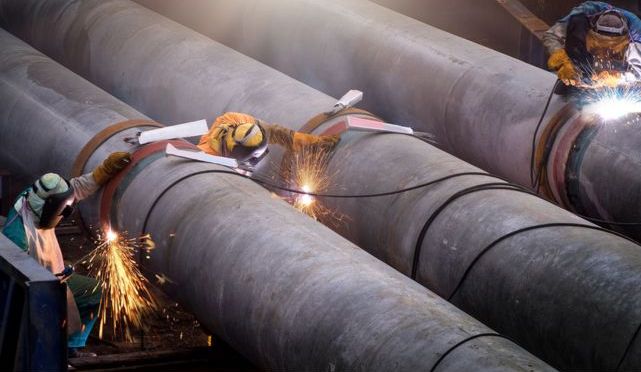
Challenges in Welding Operations for Oil and Gas Projects
Welding in the oil and gas industry presents several challenges that need to be overcome for successful operations. These challenges include:
Extreme conditions and environments
Oil and gas operations often take place in harsh and extreme environments, such as offshore platforms, arctic regions, or desert areas. Welding under extreme temperatures, high humidity, or corrosive atmospheres requires specialized techniques and equipment to ensure proper weld quality and integrity.
Complexities of working with various materials
The industry utilizes a wide range of materials, including different grades of steel, alloys, and exotic metals. Each material has its own welding characteristics, such as melting points, thermal expansion rates, and susceptibility to cracking. Welders must have a deep understanding of these materials and employ appropriate welding techniques and procedures.
High-pressure and high-temperature environments
Pipelines and pressure vessels in the oil and gas industry are subjected to high pressures and temperatures. Welding joints in these applications must withstand the internal forces and thermal stresses. Specialized welding procedures and materials, such as preheating and post-weld heat treatment, are employed to ensure the integrity and strength of these critical welds.
Corrosion and degradation factors
The presence of corrosive substances, such as hydrogen sulfide and saltwater, poses a significant challenge to welding in the oil and gas industry. Corrosion can weaken welds over time, leading to leaks or structural failures. Proper material selection, surface preparation, and corrosion-resistant welding techniques, such as alloy overlays or cladding, are crucial for mitigating the effects of corrosion.
Safety considerations and risk management
Welding in the oil and gas industry carries inherent safety risks. Welders work in hazardous environments, dealing with flammable materials, high voltages, and potential exposure to toxic gases. Adequate safety measures, including personal protective equipment (PPE), gas monitoring systems, and comprehensive training programs, are essential to protect the health and safety of welders and other personnel involved in the welding operations.
Welding Techniques for Different Pipeline Materials
In the oil and gas industry, different pipeline materials require specific welding techniques to ensure the integrity and longevity of the welds. Here are some key welding techniques for different pipeline materials:
Welding methods for steel pipelines:
Steel is commonly used in pipeline construction due to its strength and durability. The most commonly employed welding methods for steel pipelines include:
Shielded Metal Arc Welding (SMAW): Also known as stick welding, SMAW uses a coated electrode to create the weld joint. It is a versatile and widely used technique for pipeline welding.
Gas Metal Arc Welding (GMAW): Also referred to as MIG/MAG welding, GMAW utilizes a consumable wire electrode and shielding gas to protect the weld pool from atmospheric contamination.
Flux-Cored Arc Welding (FCAW): FCAW is similar to GMAW but employs a tubular electrode filled with flux. This technique provides better performance in windy or outdoor environments.
Welding challenges and techniques for alloy materials
The oil and gas industry often employs alloy materials, such as stainless steel or nickel-based alloys, to withstand corrosive or high-temperature environments. Welding these materials requires specific considerations, such as:
Preheating and post-weld heat treatment: Many alloy materials have higher thermal expansion rates and are susceptible to cracking. Preheating the base metal before welding and applying post-weld heat treatment can reduce residual stresses and improve weld integrity.
Matching filler materials: Selecting appropriate filler materials with similar alloy compositions is crucial to maintain the corrosion resistance and mechanical properties of the welded joint.
Joining techniques for dissimilar materials
In certain cases, pipelines may require joining dissimilar materials, such as steel to stainless steel or steel to non-ferrous alloys. Some commonly employed techniques for joining dissimilar materials include:
Transition joints: Transition joints are used to connect two different materials, often through a combination of welding and mechanical fastening or adhesive bonding.
Explosive welding: This specialized technique utilizes controlled explosive energy to bond dissimilar materials at the atomic level. It is particularly suitable for joining materials with significantly different properties.
Special considerations for welding in corrosive environments
Corrosive environments, such as those containing hydrogen sulfide or saltwater, pose challenges for welding. Some considerations for welding in corrosive environments include:
Corrosion-resistant welding techniques: Employing corrosion-resistant welding processes, such as alloy overlays or cladding, can provide an additional layer of protection against corrosion.
Proper surface preparation: Thorough cleaning and preparation of the base metal surfaces before welding help remove contaminants that can accelerate corrosion.
Emerging materials and their welding requirements
With ongoing technological advancements, new materials are being introduced to the oil and gas industry. Each material comes with its own unique welding requirements, including specific welding techniques, consumables, and heat treatment processes. Staying up-to-date with the latest research and industry guidelines is crucial when working with emerging materials.
By employing the appropriate welding techniques for different pipeline materials, the oil and gas industry can ensure the structural integrity and longevity of its pipelines, facilitating the safe and efficient transportation of energy resources.
Welding Techniques for Different Pipeline Materials
In the oil and gas industry, different pipeline materials require specific welding techniques to ensure the integrity and longevity of the welds. Here are some key welding techniques for different pipeline materials:
Welding methods for steel pipelines
Steel is commonly used in pipeline construction due to its strength and durability. The most commonly employed welding methods for steel pipelines include:
Shielded Metal Arc Welding (SMAW): Also known as stick welding, SMAW uses a coated electrode to create the weld joint. It is a versatile and widely used technique for pipeline welding.
Gas Metal Arc Welding (GMAW): Also referred to as MIG/MAG welding, GMAW utilizes a consumable wire electrode and shielding gas to protect the weld pool from atmospheric contamination.
Flux-Cored Arc Welding (FCAW): FCAW is similar to GMAW but employs a tubular electrode filled with flux. This technique provides better performance in windy or outdoor environments.
Welding challenges and techniques for alloy materials
The oil and gas industry often employs alloy materials, such as stainless steel or nickel-based alloys, to withstand corrosive or high-temperature environments. Welding these materials requires specific considerations, such as:
Preheating and post-weld heat treatment: Many alloy materials have higher thermal expansion rates and are susceptible to cracking. Preheating the base metal before welding and applying post-weld heat treatment can reduce residual stresses and improve weld integrity.
Matching filler materials: Selecting appropriate filler materials with similar alloy compositions is crucial to maintain the corrosion resistance and mechanical properties of the welded joint.
Joining techniques for dissimilar materials
In certain cases, pipelines may require joining dissimilar materials, such as steel to stainless steel or steel to non-ferrous alloys. Some commonly employed techniques for joining dissimilar materials include:
Transition joints: Transition joints are used to connect two different materials, often through a combination of welding and mechanical fastening or adhesive bonding.
Explosive welding: This specialized technique utilizes controlled explosive energy to bond dissimilar materials at the atomic level. It is particularly suitable for joining materials with significantly different properties.
Special considerations for welding in corrosive environments
Corrosive environments, such as those containing hydrogen sulfide or saltwater, pose challenges for welding. Some considerations for welding in corrosive environments include:
Corrosion-resistant welding techniques: Employing corrosion-resistant welding processes, such as alloy overlays or cladding, can provide an additional layer of protection against corrosion.
Proper surface preparation: Thorough cleaning and preparation of the base metal surfaces before welding help remove contaminants that can accelerate corrosion.
Emerging materials and their welding requirements
With ongoing technological advancements, new materials are being introduced to the oil and gas industry. Each material comes with its own unique welding requirements, including specific welding techniques, consumables, and heat treatment processes. Staying up-to-date with the latest research and industry guidelines is crucial when working with emerging materials.
Welding Procedures and Standards in the Oil and Gas Sector
Welding procedures and standards play a vital role in ensuring the quality and safety of welding operations in the oil and gas sector. Here are key aspects related to welding procedures and standards:
Welding procedure specifications (WPS)
Welding procedure specifications outline the specific steps and requirements for performing a particular weld. WPS documents provide detailed instructions on welding parameters, joint preparation, preheating, welding techniques, and post-weld heat treatment. These specifications are developed based on industry standards and project-specific requirements.
Qualification requirements for welders and welding procedures
To maintain quality and consistency in welding, welders and welding procedures need to be qualified. Qualification involves testing welders’ skills and knowledge to ensure they meet specific criteria, such as welding processes, positions, and materials. Similarly, welding procedures are also qualified to demonstrate their ability to produce sound welds. Qualification tests include visual inspection, mechanical testing, and sometimes non-destructive testing (NDT) methods.
Industry standards and codes for welding in oil and gas projects
The oil and gas industry follows established industry standards and codes to ensure weld quality, safety, and compliance with regulatory requirements. Standards and codes provide guidelines for material selection, welding techniques, inspection methods, and quality control. Some commonly used standards and codes in the industry include those from organizations like the American Welding Society (AWS), the American Society of Mechanical Engineers (ASME), and the International Organization for Standardization (ISO).
Quality control and inspection protocols
Quality control and inspection protocols are implemented throughout the welding process to monitor and assess weld quality. This includes various activities such as visual inspection, NDT techniques (e.g., ultrasonic testing, radiographic testing), dimensional checks, and destructive testing. Quality control personnel ensure that welding procedures are followed correctly, welds are defect-free, and project specifications and standards are met.
Advances in Welding Equipment and Technology
Advances in welding equipment and technology have revolutionized the way welding is performed in various industries, including the oil and gas sector. Let’s explore some key advancements:
Introduction of advanced welding equipment and tools
Modern welding equipment has become more sophisticated, efficient, and user-friendly. Advancements include the development of advanced power sources, such as inverter-based welding machines, which provide greater control over the welding process and improve arc stability. Additionally, portable welding equipment and compact welding systems have made it easier to access and perform welding in remote or challenging locations.
Automation and robotics in oil and gas welding
Automation and robotics have transformed welding operations in the oil and gas industry. Robotic welding systems offer increased precision, consistency, and productivity. They can perform repetitive welding tasks with high accuracy, reducing human error and improving efficiency. Automated welding systems are particularly beneficial for large-scale pipeline construction, offshore platform fabrication, and other complex welding projects.
Laser welding and its applications in the industry
Laser welding has gained prominence in the oil and gas sector due to its unique capabilities. It offers high energy density, precise control, and minimal heat input, making it suitable for welding thin materials, dissimilar materials, and complex geometries. Laser welding provides faster welding speeds, reduced distortion, and superior weld quality compared to traditional welding methods, making it a preferred choice in certain applications.
Advances in filler materials and consumables
The development of advanced filler materials and consumables has enhanced the quality and efficiency of welding processes. Specialized filler wires, fluxes, and shielding gases are designed to improve weld properties, increase productivity, and reduce defects. For example, the introduction of flux-cored wires with improved flux formulations has facilitated higher deposition rates and improved weld quality in various oil and gas welding applications.
Integration of welding with digital technologies (e.g., IoT, AI)
The integration of welding with digital technologies has opened new possibilities for process optimization and quality control. IoT (Internet of Things) enables the collection and analysis of real-time data from welding equipment, allowing for remote monitoring, predictive maintenance, and performance optimization. Artificial Intelligence (AI) algorithms can analyze welding data to identify patterns, optimize process parameters, and improve weld quality.
Non-Destructive Testing (NDT) Methods for Weld Quality Assessment
Non-Destructive Testing (NDT) methods are crucial for assessing the quality of welds in the oil and gas industry. Let’s explore some key aspects related to NDT in weld quality assessment:
Importance of NDT in ensuring weld quality
NDT plays a vital role in verifying the integrity of welded joints without causing damage to the tested components. It helps identify any defects or discontinuities that may compromise the structural integrity or functionality of the weld. NDT is essential for ensuring that welds meet industry standards, codes, and project requirements.
Common NDT techniques used in the oil and gas industry
The oil and gas sector utilizes various NDT techniques to assess weld quality. Some commonly employed methods include:
Ultrasonic Testing (UT): UT uses high-frequency sound waves to detect internal and surface defects in welds. It provides detailed information about the size, location, and orientation of flaws, such as cracks, lack of fusion, or porosity.
Radiographic Testing (RT): RT involves exposing a weld to X-rays or gamma rays and capturing the resulting image on film or digitally. It enables the detection of internal defects, such as cracks, inclusions, or voids.
Magnetic Particle Testing (MT): MT is primarily used for detecting surface-breaking defects in ferromagnetic materials. It involves the application of magnetic fields and magnetic particles to identify cracks or discontinuities.
Liquid Penetrant Testing (PT): PT is employed to detect surface defects in welds. It involves the application of a colored or fluorescent liquid penetrant that seeps into surface discontinuities, making them visible under proper lighting conditions.
Ultrasonic testing, radiographic testing, and other methods
Ultrasonic testing and radiographic testing are particularly valuable in assessing weld quality. UT provides detailed information about the internal structure and dimensions of welds, while RT allows for the detection of both internal and external defects. Other NDT methods, such as MT and PT, focus on surface defects and are effective in identifying cracks, porosity, or lack of fusion.
Weld inspection and defect detection techniques
NDT methods are employed to inspect welds and identify various welding defects, including cracks, lack of fusion, porosity, undercutting, and incomplete penetration. Skilled NDT technicians perform visual inspections to identify surface imperfections and then utilize appropriate NDT techniques to further assess the weld quality and detect hidden defects.
Proper implementation of NDT techniques ensures that welds meet the required quality standards, enhances the overall reliability of welded components, and helps prevent costly failures or accidents in the oil and gas industry. NDT serves as an essential tool in quality assurance and contributes to the longevity and safety of infrastructure in the sector.
Welding Safety Measures and Risk Mitigation
Ensuring safety in welding operations is of utmost importance in the oil and gas industry. Here are key considerations for welding safety measures and risk mitigation:
Personal protective equipment (PPE) for welders
Welders must use appropriate PPE to protect themselves from potential hazards. This includes wearing protective clothing, such as flame-resistant jackets and pants, gloves, welding helmets with appropriate filters, safety glasses or goggles, and steel-toed boots. PPE helps safeguard against sparks, ultraviolet radiation, heat, and potential flying debris.
Hazard identification and risk assessment in welding operations
Prior to commencing any welding operation, a thorough hazard identification and risk assessment should be conducted. This involves identifying potential hazards, such as fire, explosions, electric shock, toxic fumes, and the risk of falling objects. Assessing the risks allows for the implementation of appropriate control measures to mitigate them.
Fire prevention and control measures
Welding operations involve the use of heat, sparks, and flammable materials, which can lead to fire hazards. Implementing fire prevention and control measures is essential. This includes having fire extinguishers readily available, ensuring proper ventilation in confined spaces, removing flammable materials from the work area, and having trained personnel who are familiar with fire response procedures.
Training and certification requirements for welders
Welders should receive adequate training and possess relevant certifications to demonstrate their competency in performing welding tasks safely. Training programs should cover topics such as welding techniques, equipment operation, hazard recognition, PPE usage, and emergency procedures. Certification programs, such as those offered by recognized organizations like the AWS, provide validation of a welder’s skills and knowledge.
Emergency response planning and protocols
Having comprehensive emergency response plans and protocols in place is crucial. These plans should address potential emergencies, such as fires, explosions, injuries, or releases of hazardous substances. They should include procedures for evacuations, first aid, fire control, and communication. Regular drills and training sessions should be conducted to ensure all personnel are familiar with the emergency response protocols.
Future Trends and Innovations in Oil and Gas Welding
Research and development initiatives in welding technology
Ongoing research and development efforts focus on improving welding techniques, equipment, and materials used in the industry. This includes advancements in arc welding processes, development of new welding technologies (such as friction stir welding and laser welding), and the exploration of innovative filler materials and consumables.
Predictive maintenance and condition monitoring of welds
The integration of sensors, data analytics, and machine learning enables the implementation of predictive maintenance strategies for welds. By continuously monitoring weld conditions and performance, potential defects or failures can be detected early, allowing for timely maintenance and repairs. This approach helps to optimize asset integrity, reduce downtime, and enhance overall operational efficiency.
Integration of AI and machine learning in welding processes
Artificial Intelligence (AI) and machine learning are being applied to welding processes to optimize parameters, improve weld quality, and automate certain aspects of welding operations. AI algorithms can analyze vast amounts of data, such as weld characteristics, process parameters, and inspection results, to optimize welding parameters and improve efficiency. Machine learning techniques enable the development of intelligent systems capable of self-adjustment and adaptive control during welding operations.
Sustainability and environmental considerations in welding
With increasing environmental awareness, there is a growing emphasis on sustainability in welding processes. Efforts are being made to minimize the environmental impact of welding operations, such as reducing energy consumption, optimizing material usage, and exploring environmentally friendly alternatives. This includes the development of low-carbon and low-emission welding processes, as well as the use of recycled materials and eco-friendly consumables.
FAQs
Which welding is used in oil and gas industry?
The most commonly used welding techniques in the oil and gas industry include Shielded Metal Arc Welding (SMAW), Gas Tungsten Arc Welding (GTAW), and Flux-Cored Arc Welding (FCAW).
What are the 4 main types of welding?
The four main types of welding are: a. Gas Metal Arc Welding (GMAW/MIG) b. Shielded Metal Arc Welding (SMAW/MMA) c. Gas Tungsten Arc Welding (GTAW/TIG) d. Flux-Cored Arc Welding (FCAW)
What do welders do in the oil field?
Welders in the oil field perform a range of tasks related to welding and joining metal components. They may be involved in welding pipelines, fabricating structures, repairing equipment, conducting inspections, and ensuring weld quality and integrity.
What type of welding is used in pipelines?
In pipelines, the most commonly used welding technique is Shielded Metal Arc Welding (SMAW), also known as Manual Metal Arc Welding (MMAW) or “stick welding.” Other techniques like Gas Metal Arc Welding (GMAW/MIG) and Flux-Cored Arc Welding (FCAW) may also be used depending on the specific requirements.
What is an oil welder?
An oil welder is a welder who specializes in performing welding operations in the oil industry. They are responsible for welding pipelines, oil rigs, storage tanks, and other oil-related infrastructure.
What are the duties of a welder?
The duties of a welder can include interpreting blueprints, preparing metal surfaces, operating welding equipment, selecting appropriate welding techniques, assembling and welding metal components, inspecting welds for quality and accuracy, and maintaining welding equipment.
What are the 3 main types of welding?
The three main types of welding are: a. Arc Welding (including SMAW/MMA, GTAW/TIG, and FCAW) b. Resistance Welding (including Spot Welding and Seam Welding) c. Gas Welding (including Oxy-Acetylene Welding)
Conclusion
In conclusion, welding plays a critical role in the oil and gas industry, enabling the production and transportation of energy resources while ensuring the integrity of infrastructure. However, welding in this sector comes with its own set of challenges, including extreme conditions, complex materials, high pressures and temperatures, corrosion, and safety risks.
To overcome these challenges, various welding techniques have been developed, tailored to different pipeline materials such as steel, alloys, and dissimilar materials. Special considerations are also given to welding in corrosive environments, with emerging materials requiring specific welding requirements.
Furthermore, welding procedures and standards are established to maintain quality and safety in oil and gas projects. Welding procedure specifications, qualification requirements for welders and procedures, as well as industry standards and codes, guide the welding processes. Quality control and inspection protocols ensure adherence to these standards.
Advancements in welding equipment and technology continue to shape the industry. With the introduction of advanced equipment, automation, laser welding, and integration with digital technologies, welding processes have become more efficient, precise, and reliable. Predictive maintenance, condition monitoring, and the use of AI and machine learning further enhance weld quality and optimize operations.
Safety measures and risk mitigation are paramount in welding operations. Personal protective equipment, hazard identification, fire prevention, training, and emergency response planning are essential components in ensuring the well-being of welders and the prevention of accidents.
Looking ahead, future trends in oil and gas welding include ongoing research and development initiatives, predictive maintenance, AI integration, and sustainability considerations. These advancements aim to improve welding technologies, optimize asset integrity, reduce environmental impact, and address evolving industry needs.
In conclusion, by embracing these advancements, adhering to standards, prioritizing safety, and staying at the forefront of technological innovations, the oil and gas industry can continue to enhance weld quality, increase operational efficiency, and ensure the long-term integrity and reliability of infrastructure.