Hydrogen Embrittlement in Welding
Hydrogen embrittlement is a critical concern in the welding industry, impacting the integrity and performance of welded structures. In this article, we delve into the phenomenon of hydrogen embrittlement, its causes, preventive measures, and its influence on various welding techniques. By understanding the complexities of hydrogen embrittlement, welders, engineers, and industries can implement strategies to mitigate its detrimental effects on welded components.
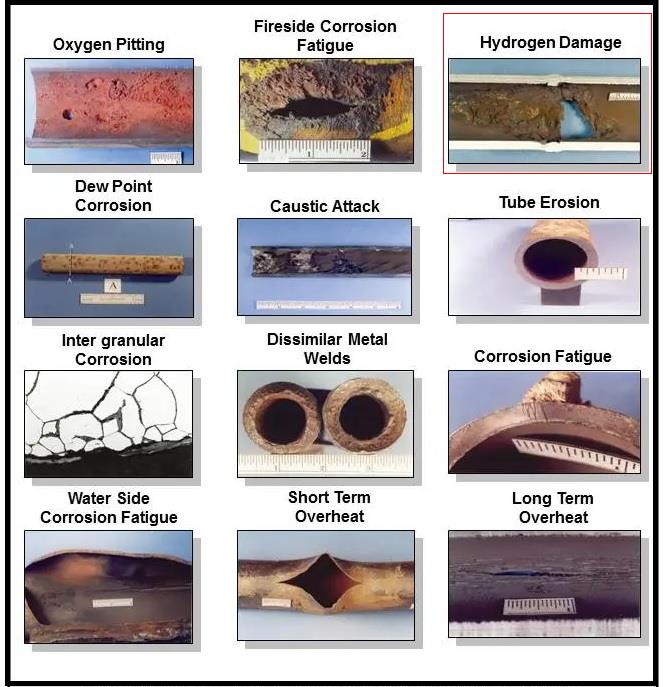
Introduction
Welding is a widely used method for joining metals in various industries, ranging from construction and manufacturing to aerospace and automotive. While welding provides strong and durable connections, it also introduces the risk of hydrogen embrittlement. This phenomenon occurs when hydrogen atoms infiltrate the metal’s lattice structure, leading to increased brittleness and reduced mechanical properties.
Understanding Hydrogen Embrittlement
What is Hydrogen Embrittlement?
Hydrogen embrittlement is a process where hydrogen atoms, typically from external sources, penetrate the metal’s grain boundaries during or after welding. Once inside, hydrogen can accumulate at high-stress regions, such as notches or cracks, leading to embrittlement and potential failure under mechanical loads.
Causes of Hydrogen Embrittlement
Hydrogen can enter the metal during welding through various means, including:
- Moisture Contamination: Water vapor can dissociate into hydrogen and oxygen during the welding process, and hydrogen gets absorbed by the metal.
- Electrolytic Processes: Electrolytic environments, such as acids or salts, can produce hydrogen as a byproduct, which can diffuse into metals.
- Hydrogen-Containing Fluxes and Shielding Gases: Some welding processes use fluxes and shielding gases that contain hydrogen, increasing the risk of embrittlement.
The Role of Hydrogen in Welding
In welding, hydrogen can have a detrimental impact on the material’s properties. It reduces ductility, lowers impact toughness, and increases susceptibility to cracking, leading to potential catastrophic failures if not addressed.
Types of Hydrogen Embrittlement
Hydrogen embrittlement can be categorized into two types:
Internal Hydrogen Embrittlement
Internal hydrogen embrittlement occurs when hydrogen is present within the material before welding. It can be a result of material processing, such as hydrogen contamination during manufacturing or hydrogen absorbed during storage.
External Hydrogen Embrittlement
External hydrogen embrittlement takes place when hydrogen is introduced to the material during or after welding. This type is often a consequence of the welding process itself, as well as the surrounding environment.
Factors Affecting Hydrogen Embrittlement in Welding
The susceptibility to hydrogen embrittlement depends on various factors, including:
Material Composition
Certain materials, such as high-strength steels, are more prone to hydrogen embrittlement due to their microstructure and chemical composition.
Temperature and Pressure
Higher temperatures and pressures can enhance the diffusion of hydrogen into the metal, increasing the risk of embrittlement.
Welding Processes
Different welding techniques have varying levels of hydrogen exposure, with some processes being more susceptible to introducing hydrogen into the material.
Preventive Measures for Hydrogen Embrittlement
Preventing hydrogen embrittlement requires a comprehensive approach, including:
Preheating
Preheating the material before welding can reduce the cooling rate and decrease hydrogen diffusion, minimizing the risk of embrittlement.
Post-weld Heat Treatment
Applying heat treatment after welding can help diffuse hydrogen out of the metal, restoring its mechanical properties.
Material Selection
Choosing materials with low hydrogen susceptibility and adequate toughness properties can mitigate embrittlement risks.
Hydrogen-Induced Cracking Testing
Performing non-destructive testing to identify hydrogen-induced cracks before they lead to catastrophic failures.
Hydrogen Embrittlement in Specific Welding Techniques
Different welding techniques present unique challenges regarding hydrogen embrittlement. Let’s explore a few common methods:
Gas Tungsten Arc Welding (GTAW)
GTAW, also known as TIG welding, utilizes a non-consumable tungsten electrode and inert shielding gas. While this process generally has low hydrogen content, proper gas selection and control are crucial to prevent embrittlement.
Shielded Metal Arc Welding (SMAW)
SMAW, or stick welding, involves a flux-coated consumable electrode. The flux may contain hydrogen, making it vital to select low-hydrogen electrodes and use appropriate drying techniques.
Gas Metal Arc Welding (GMAW)
GMAW, or MIG welding, employs a continuously fed wire electrode and shielding gas. Choosing the right shielding gas and ensuring its dryness is essential in mitigating hydrogen-related issues.
Flux-Cored Arc Welding (FCAW)
FCAW utilizes a tubular wire electrode filled with flux. Similar to other processes, it’s crucial to control the hydrogen content in the flux to avoid embrittlement.
Industry Standards and Regulations
The welding industry adheres to several standards and regulations to address hydrogen embrittlement concerns:
American Welding Society (AWS)
The AWS provides guidelines and recommendations for welding procedures and materials to minimize hydrogen-related issues.
International Institute of Welding (IIW)
IIW promotes best practices in welding and offers guidance on handling hydrogen embrittlement in different applications.
American Society for Testing and Materials (ASTM)
ASTM establishes testing methods and material specifications to prevent hydrogen-induced cracking.
Case Studies of Hydrogen Embrittlement Failures
Several industries have experienced hydrogen embrittlement-related failures:
Oil and Gas Industry
Hydrogen embrittlement in oil and gas pipelines has led to leaks and ruptures, highlighting the importance of preventive measures.
Automotive Industry
Certain automotive components, like high-strength bolts, have been susceptible to hydrogen embrittlement failures.
Aerospace Industry
Aerospace components must undergo rigorous testing and mitigation strategies to prevent hydrogen-related failures.
Mitigating Hydrogen Embrittlement Risks in Real-World Applications
Hydrogen embrittlement poses significant challenges in specific applications:
Offshore Structures
Offshore platforms and structures require advanced materials and welding techniques to combat hydrogen embrittlement in corrosive environments.
Pressure Vessels
Pressure vessels must undergo thorough testing and meet strict material requirements to ensure long-term performance.
Pipelines
Pipelines carrying hazardous materials must be designed and constructed with measures to avoid hydrogen-induced cracking.
Future Research and Innovations
To further address hydrogen embrittlement, ongoing research focuses on:
Novel Welding Techniques
Developing welding processes with reduced hydrogen exposure and improved mechanical properties.
Material Design and Development
Creating materials that are inherently resistant to hydrogen embrittlement while maintaining their structural integrity.
Conclusion
Hydrogen embrittlement is a complex and critical concern in welding applications. By understanding the causes and preventive measures, industries can reduce the risk of hydrogen-induced failures. Implementing appropriate welding techniques, adhering to industry standards, and conducting rigorous testing are crucial steps toward ensuring the integrity and safety of welded structures.
FAQs
Is hydrogen embrittlement reversible?
No, hydrogen embrittlement is generally irreversible, and once it has affected the material, its mechanical properties cannot be fully restored.
Can hydrogen embrittlement be completely eliminated?
While complete elimination is challenging, the risk of hydrogen embrittlement can be significantly reduced through careful material selection, welding practices, and testing.
Are all metals susceptible to hydrogen embrittlement?
No, not all metals are equally susceptible. High-strength steels and certain alloys are more prone to hydrogen embrittlement.
What industries are most affected by hydrogen embrittlement?
The oil and gas, automotive, and aerospace industries are particularly affected due to their extensive use of welded components.
How often should hydrogen-induced cracking testing be conducted?
The frequency of testing depends on the application and industry standards, but it is typically performed during material qualification and at regular intervals during service life.