Pressure Vessel Welding Standards
Ensuring Safety and Reliability
Introduction
Pressure vessels play a critical role in various industries, including oil and gas, chemical, power generation, and many others. These vessels are designed to contain fluids or gases at a pressure significantly different from the ambient pressure. As such, their construction and welding must adhere to strict standards to ensure safety, reliability, and optimal performance.
Overview of Pressure Vessel Welding Standards
National and international standards organizations:
Pressure vessel welding standards are developed and maintained by various national and international standards organizations. These organizations play a crucial role in setting guidelines, codes, and regulations to ensure the safe and reliable fabrication of pressure vessels. Some prominent organizations involved in the development of welding standards include:
- American Society of Mechanical Engineers (ASME): ASME is a well-known organization responsible for developing and publishing the ASME Boiler and Pressure Vessel Code (BPVC). The BPVC provides comprehensive standards for the design, construction, and inspection of pressure vessels, including welding requirements.
- American Welding Society (AWS): AWS is a leading organization in the field of welding. They develop and publish a wide range of standards related to welding processes, procedures, qualifications, and inspection. Their standards provide guidance on welding practices and qualifications for pressure vessel fabrication.
- European Committee for Standardization (CEN): CEN develops and publishes European standards (EN) for various industries, including pressure vessel welding. These standards are widely used across European countries and are intended to harmonize requirements for pressure vessel fabrication.
Commonly referenced standards for pressure vessel welding:
Several commonly referenced standards are specifically dedicated to pressure vessel welding. These standards provide detailed guidelines for welding procedures, welder qualifications, inspection, and other essential aspects. Some widely recognized standards for pressure vessel welding include:
- ASME Boiler and Pressure Vessel Code (BPVC): The ASME BPVC is a comprehensive code that covers various aspects of pressure vessel design, construction, and inspection. It includes specific sections, such as Section IX, which focuses on welding and brazing qualifications. This code is widely adopted in North America and many other parts of the world.
- American Welding Society (AWS) standards: AWS develops numerous standards related to welding, including those applicable to pressure vessel fabrication. For example, AWS D1.1 provides guidelines for structural welding, and AWS D1.6 focuses on welding stainless steel. These standards address welding procedures, qualification requirements, and quality control measures.
- European Pressure Equipment Directive (PED): The PED is a European Union directive that outlines essential safety requirements for pressure equipment, including pressure vessels. It sets harmonized standards for the design, fabrication, and conformity assessment of pressure vessels within the European Economic Area (EEA).
- ISO standards: The International Organization for Standardization (ISO) develops a wide range of standards applicable to pressure vessel welding. ISO 3834 provides requirements for quality management in welding, while ISO 9606 defines the qualification testing of welders. ISO 15614-1 specifies the procedure qualification for arc welding of metallic materials.
These standards are recognized globally and serve as important references for pressure vessel welding practices. Manufacturers, welders, and inspectors often rely on these standards to ensure compliance, maintain quality, and meet industry requirements. It is essential to consult and follow the appropriate standards based on the specific jurisdiction, industry, and project requirements.
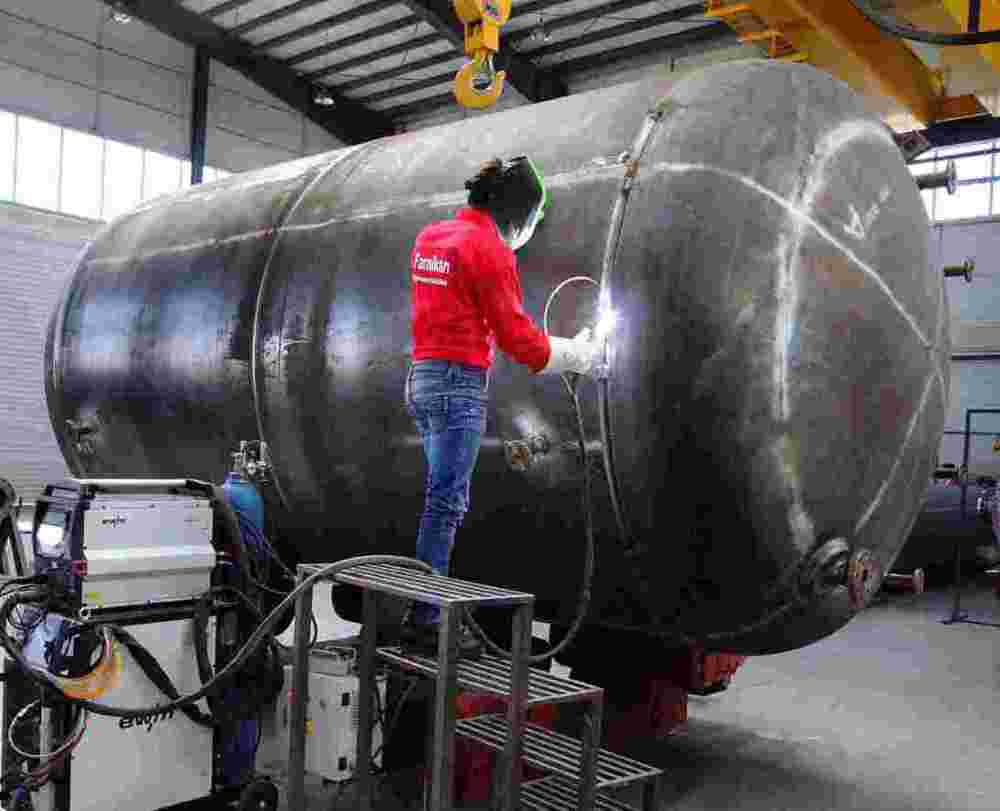
Key Elements of Pressure Vessel Welding Standards
Welding procedure qualification:
Welding procedure qualification is a critical aspect of pressure vessel welding standards. It ensures that welding procedures used in the fabrication of pressure vessels meet specified requirements for quality, reliability, and safety. Key elements of welding procedure qualification include:
- Pre-welding activities: Before initiating welding, pre-welding activities are necessary. These include selecting appropriate materials, determining joint design, and establishing welding parameters based on the specific requirements of the pressure vessel and the welding standards being followed.
- Procedure development and qualification testing: The welding procedure development involves defining the welding technique, parameters, and essential variables that will be used during fabrication. Qualification testing is then performed to demonstrate the suitability and consistency of the welding procedure. This typically involves performing test welds and subjecting them to various inspections and tests to ensure they meet the specified standards and acceptance criteria.
- Documentation requirements: Welding procedure qualification requires comprehensive documentation to ensure traceability and repeatability. This includes maintaining records of the welding procedure specification, test results, inspection reports, and any deviations or changes made during the qualification process.
Welder qualification and certification:
Welder qualification and certification are crucial to ensure that individuals performing welding on pressure vessels possess the necessary skills, knowledge, and experience. Key elements of welder qualification and certification include:
- Skills and knowledge requirements: Welders need to demonstrate proficiency in specific welding processes and techniques relevant to pressure vessel fabrication. They should possess knowledge of welding codes and standards, material characteristics, joint design, and safety practices.
- Training and examination processes: Welder qualification typically involves a combination of formal training and practical experience. Welders may undergo training programs, apprenticeships, or vocational courses to develop the required skills. Examination processes, such as practical weld tests and written assessments, are conducted to evaluate the welder’s competency.
- Periodic requalification: To ensure ongoing competency, welder qualification may have expiration dates or require periodic requalification. This ensures that welders stay up-to-date with new techniques, materials, and standards. Periodic requalification may involve retesting or completing refresher training programs.
Welding materials and consumables:
Pressure vessel welding standards specify requirements for the selection, specifications, and acceptance of welding materials and consumables. Key elements include:
- Material selection and specifications: The standards define the types of materials suitable for pressure vessel construction and provide specifications for their chemical composition, mechanical properties, and heat treatment requirements. These requirements ensure that the selected materials can withstand the anticipated operating conditions and maintain their integrity over the vessel’s service life.
- Acceptance criteria for consumables: Welding consumables, such as filler metals and shielding gases, must meet specified quality standards. Acceptance criteria may include requirements for tensile strength, impact toughness, chemical composition, and certifications from accredited manufacturers. Adhering to these criteria ensures that consumables used in welding processes contribute to the overall quality and reliability of the pressure vessel welds.
Compliance and Enforcement of Pressure Vessel Welding Standards
Regulatory authorities and their roles:
Compliance with pressure vessel welding standards is enforced by regulatory authorities responsible for ensuring the safety and reliability of pressure vessels. The specific authorities may vary depending on the country or region. Common regulatory authorities involved in enforcing pressure vessel welding standards include:
- Occupational Safety and Health Administration (OSHA) in the United States: OSHA sets and enforces workplace safety regulations, including those related to pressure vessels. They conduct inspections, provide guidance, and take necessary enforcement actions to ensure compliance.
- National Board of Boiler and Pressure Vessel Inspectors (NBBI) in the United States: The NBBI oversees the certification and inspection of pressure vessels. They establish rules and regulations, conduct audits, and issue certifications for pressure vessel manufacturers and repair organizations.
- Health and Safety Executive (HSE) in the United Kingdom: The HSE is responsible for enforcing health and safety regulations, including those related to pressure vessels. They carry out inspections, investigations, and provide guidance to ensure compliance.
- Technical Inspection Associations in Europe: Each European country has its own Technical Inspection Association responsible for inspecting and certifying pressure vessels. These associations work in conjunction with regulatory bodies to ensure compliance with applicable standards and regulations.
Inspection and certification processes:
Inspection and certification processes play a crucial role in verifying compliance with pressure vessel welding standards. These processes involve various stages and activities, including:
- Initial inspections: Regulatory authorities and authorized inspection agencies conduct initial inspections of pressure vessels during their fabrication, installation, or commissioning stages. These inspections ensure that the vessels are constructed in accordance with approved welding procedures, materials, and standards.
- In-service inspections: Pressure vessels undergo regular in-service inspections throughout their operational life. These inspections assess the condition of the vessels, including the integrity of welds, to identify any signs of degradation, corrosion, or fatigue. Non-destructive testing techniques, such as ultrasonic testing or radiographic inspection, may be used during these inspections.
- Certification: Pressure vessel manufacturers may obtain certifications to demonstrate compliance with applicable welding standards. These certifications are often issued by authorized bodies, such as the ASME Certification Mark or the CE marking in Europe, indicating that the pressure vessels meet the required standards and have undergone necessary inspections and quality control measures.
Consequences of non-compliance:
Non-compliance with pressure vessel welding standards can have significant consequences, including:
- Safety risks: Failure to adhere to welding standards can compromise the structural integrity of pressure vessels, leading to leaks, rupture, or catastrophic failures. This poses severe safety risks to personnel, property, and the environment.
- Legal implications: Non-compliance with welding standards can result in legal consequences, including fines, penalties, or legal action. Regulatory authorities have the power to issue compliance notices, suspend operations, or even initiate criminal charges for serious breaches.
- Reputational damage: Non-compliance with welding standards can damage the reputation of pressure vessel manufacturers and operators. This can lead to loss of trust from customers, stakeholders, and regulatory bodies, impacting business opportunities and relationships.
- Financial losses: Correcting non-compliant welds and bringing pressure vessels up to code can be costly. Non-compliance may require repairs, modifications, or even replacement of pressure vessels, leading to financial losses for manufacturers and operators.
Welding Techniques for Pressure Vessels
Pressure vessel welding involves several techniques, each with its advantages and limitations. The choice of welding method depends on factors such as material type, thickness, and design considerations. Here are some commonly used welding techniques for pressure vessels:
Shielded Metal Arc Welding (SMAW)
SMAW, also known as stick welding, is a widely used welding process for pressure vessels. It utilizes a consumable electrode coated with flux, which provides shielding gas and forms a slag to protect the weld pool. SMAW is versatile and can be used with various materials and thicknesses. However, it is relatively slow compared to other methods.
Gas Metal Arc Welding (GMAW)
GMAW, commonly known as MIG (Metal Inert Gas) or MAG (Metal Active Gas) welding, is a popular choice for pressure vessel fabrication. It uses a continuous wire electrode and a shielding gas to protect the weld from atmospheric contamination. GMAW offers high deposition rates and is suitable for both thin and thick materials.
Flux-Cored Arc Welding (FCAW)
FCAW is similar to GMAW but uses a tubular electrode filled with flux. The flux provides shielding and generates a slag, improving the weld quality. FCAW is known for its high productivity and excellent penetration capabilities. It is commonly used for welding thick materials and in outdoor or windy conditions.
Submerged Arc Welding (SAW)
SAW is an efficient welding process suitable for welding thick sections of pressure vessels. It utilizes a continuously fed electrode and a granular flux, which covers the weld pool completely. SAW is known for its high deposition rates, deep penetration, and excellent weld quality. However, it requires a special setup and is mainly used for fixed-position welding.
Welding Procedures and Qualifications
To ensure consistent weld quality, pressure vessel welding standards require the development and qualification of welding procedures and welders. Welding procedures (WPQR) outline the specific parameters and techniques to be used during welding. They include details such as welding process, preheat and interpass temperature, filler metal type, and post-weld heat treatment.
Welding procedures must be qualified by performing a series of tests, as specified in the welding standards. These tests evaluate the mechanical properties and soundness of the welds. Qualified welding procedures are essential to ensure the welds meet the necessary strength, ductility, and toughness requirements.
Welders involved in pressure vessel fabrication must also be qualified to perform the welding operations. Qualification tests assess the welder’s skill and ability to produce sound welds. They typically involve welding test coupons, which are then subjected to non-destructive and destructive testing to evaluate the welder’s proficiency.
Non-Destructive Testing (NDT) of Pressure Vessel Welds
Non-destructive testing (NDT) techniques are employed to examine the quality and integrity of pressure vessel welds without causing any damage. These inspections help detect potential defects or discontinuities that may compromise the vessel’s structural integrity. Some commonly used NDT methods for pressure vessel welds include:
Radiographic Testing (RT)
Radiographic testing, commonly known as X-ray testing, uses X-rays or gamma rays to create an image of the weld. This method is effective in detecting internal defects such as cracks, porosity, and lack of fusion. RT provides detailed information about the quality and integrity of the weld but requires specialized equipment and trained personnel.
Ultrasonic Testing (UT)
Ultrasonic testing utilizes high-frequency sound waves to inspect pressure vessel welds. The sound waves are transmitted into the weld, and the reflections or echoes are analyzed to detect any defects. UT is widely used due to its versatility, portability, and ability to detect both surface and subsurface defects.
Magnetic Particle Testing (MT)
Magnetic particle testing is primarily used to detect surface-breaking defects in ferromagnetic materials. The process involves magnetizing the weld area and applying iron particles with contrasting colors or fluorescent dyes. If there is a defect, the particles will be attracted to it, creating visible indications. MT is relatively quick and cost-effective for detecting surface cracks and other defects.
Liquid Penetrant Testing (PT)
Liquid penetrant testing is used to detect surface-breaking defects, including cracks, porosity, and leaks. The process involves applying a liquid penetrant to the weld surface, which seeps into any surface defects. After a specific dwell time, excess penetrant is removed, and a developer is applied to draw out the penetrant trapped in the defects. PT is simple, economical, and widely applicable to various materials.
FAQs
Are pressure vessel welding standards mandatory?
Yes, pressure vessel welding standards are mandatory to ensure the safety and reliability of pressure vessels. Adhering to these standards is a legal requirement in many countries.
What are the consequences of not following pressure vessel welding standards?
Failing to follow pressure vessel welding standards can result in weld defects, compromised structural integrity, and potentially catastrophic failures. It can also lead to legal repercussions and liabilities for the manufacturer.
Can pressure vessel welding standards be customized for specific applications?
Yes, pressure vessel welding standards can be customized to some extent to suit specific applications and industries. However, any modifications must still meet the minimum safety and quality requirements.
How often are pressure vessel welding standards updated?
Pressure vessel welding standards are periodically updated by the relevant regulatory bodies or standard organizations. Updates incorporate advancements in technology, materials, and industry best practices.
Are there international standards for pressure vessel welding?
While there is no single international standard, the ASME BPVC is widely recognized and accepted globally. Other countries may have their own national standards based on the ASME code or equivalent.
How can manufacturers ensure compliance with pressure vessel welding standards?
Manufacturers can ensure compliance by implementing robust quality management systems, conducting regular inspections and tests, and employing qualified welders. They should also stay informed about any updates or changes to the relevant standards.
Conclusion
Pressure vessel welding standards are essential to ensure the safety, reliability, and performance of these critical components in various industries. Adhering to recognized standards such as the ASME BPVC helps manufacturers produce welds of high quality and integrity. By using appropriate welding techniques, developing qualified procedures, and conducting thorough inspections, pressure vessel manufacturers can build vessels that withstand the demanding operating conditions and safeguard both human lives and the environment.